Would a grinding machine be a simple and workable propulsion system for an interplanetary spacecraft?
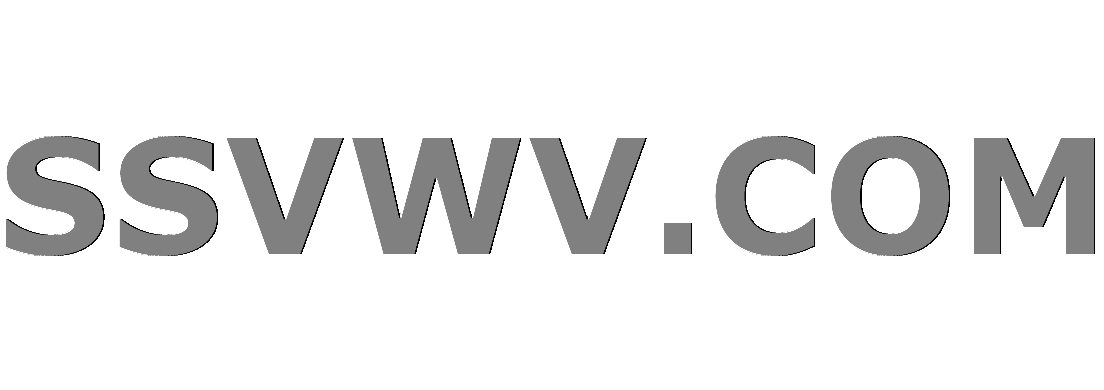
Multi tool use
$begingroup$
I am wondering if any space agency has ever considered using a grinding machine as a propulsion system for an interplanetary spacecraft. This system would not be used to lift the spacecraft off of a planet's surface, but rather used solely as an interplanetary/interstellar propulsion system.
The working principle is a simple one (see picture below). This grinding machine would be located at the stern of the spacecraft. Metal shavings flying off of the grinding wheel of this grinding machine would produce a propelling force for the spacecraft via Newton's Third Law of Motion. The amount of propulsion produced at any one time would be achieved by increasing/decreasing the rotational speed of the grinding wheel.
The electrical source for the electric motor of the grinding machine could be a small nuclear power plant on board the spacecraft. The 'fuel' source could be long steel rods or large rocks. A source of rocks could be obtained by mining an asteroid field or a small moon. Lastly, I think that diamond grinding wheels would probably be the most ideal to use due to their durability and longevity.
Would a grinding machine be a simple and workable propulsion system for an interplanetary spacecraft?
spacecraft propulsion engine-design physics design-alternative
$endgroup$
|
show 13 more comments
$begingroup$
I am wondering if any space agency has ever considered using a grinding machine as a propulsion system for an interplanetary spacecraft. This system would not be used to lift the spacecraft off of a planet's surface, but rather used solely as an interplanetary/interstellar propulsion system.
The working principle is a simple one (see picture below). This grinding machine would be located at the stern of the spacecraft. Metal shavings flying off of the grinding wheel of this grinding machine would produce a propelling force for the spacecraft via Newton's Third Law of Motion. The amount of propulsion produced at any one time would be achieved by increasing/decreasing the rotational speed of the grinding wheel.
The electrical source for the electric motor of the grinding machine could be a small nuclear power plant on board the spacecraft. The 'fuel' source could be long steel rods or large rocks. A source of rocks could be obtained by mining an asteroid field or a small moon. Lastly, I think that diamond grinding wheels would probably be the most ideal to use due to their durability and longevity.
Would a grinding machine be a simple and workable propulsion system for an interplanetary spacecraft?
spacecraft propulsion engine-design physics design-alternative
$endgroup$
12
$begingroup$
It would need 2 grinding machines for a counter balance.
$endgroup$
– Muze
Mar 30 at 21:58
18
$begingroup$
"The amount of propulsion produced at any one time would be achieved by increasing/decreasing the rotational speed of the grinding wheel." -- More likely, by utilizing a duty cycle of 100% on/off, otherwise you're wasting your fuel by not ejecting it with full force.
$endgroup$
– Jacob Krall
Mar 31 at 4:33
1
$begingroup$
@JacobKrall good point, or just by varying the feed rate of the work piece against the wheel.
$endgroup$
– uhoh
Mar 31 at 6:39
2
$begingroup$
What are you using to power the wheel? Why don't you use that to power the ship directly?
$endgroup$
– David Richerby
Apr 1 at 11:24
1
$begingroup$
FWIW: youtu.be/SAHmTQWsxeM?t=171Lighter Exhaust Gas == Higher Velocity
(at the same temperature). I'm guessing that would also apply to solids.
$endgroup$
– PEEJWEEJ
Apr 1 at 16:00
|
show 13 more comments
$begingroup$
I am wondering if any space agency has ever considered using a grinding machine as a propulsion system for an interplanetary spacecraft. This system would not be used to lift the spacecraft off of a planet's surface, but rather used solely as an interplanetary/interstellar propulsion system.
The working principle is a simple one (see picture below). This grinding machine would be located at the stern of the spacecraft. Metal shavings flying off of the grinding wheel of this grinding machine would produce a propelling force for the spacecraft via Newton's Third Law of Motion. The amount of propulsion produced at any one time would be achieved by increasing/decreasing the rotational speed of the grinding wheel.
The electrical source for the electric motor of the grinding machine could be a small nuclear power plant on board the spacecraft. The 'fuel' source could be long steel rods or large rocks. A source of rocks could be obtained by mining an asteroid field or a small moon. Lastly, I think that diamond grinding wheels would probably be the most ideal to use due to their durability and longevity.
Would a grinding machine be a simple and workable propulsion system for an interplanetary spacecraft?
spacecraft propulsion engine-design physics design-alternative
$endgroup$
I am wondering if any space agency has ever considered using a grinding machine as a propulsion system for an interplanetary spacecraft. This system would not be used to lift the spacecraft off of a planet's surface, but rather used solely as an interplanetary/interstellar propulsion system.
The working principle is a simple one (see picture below). This grinding machine would be located at the stern of the spacecraft. Metal shavings flying off of the grinding wheel of this grinding machine would produce a propelling force for the spacecraft via Newton's Third Law of Motion. The amount of propulsion produced at any one time would be achieved by increasing/decreasing the rotational speed of the grinding wheel.
The electrical source for the electric motor of the grinding machine could be a small nuclear power plant on board the spacecraft. The 'fuel' source could be long steel rods or large rocks. A source of rocks could be obtained by mining an asteroid field or a small moon. Lastly, I think that diamond grinding wheels would probably be the most ideal to use due to their durability and longevity.
Would a grinding machine be a simple and workable propulsion system for an interplanetary spacecraft?
spacecraft propulsion engine-design physics design-alternative
spacecraft propulsion engine-design physics design-alternative
edited Mar 31 at 0:00
HRIATEXP
asked Mar 30 at 20:56
HRIATEXPHRIATEXP
28819
28819
12
$begingroup$
It would need 2 grinding machines for a counter balance.
$endgroup$
– Muze
Mar 30 at 21:58
18
$begingroup$
"The amount of propulsion produced at any one time would be achieved by increasing/decreasing the rotational speed of the grinding wheel." -- More likely, by utilizing a duty cycle of 100% on/off, otherwise you're wasting your fuel by not ejecting it with full force.
$endgroup$
– Jacob Krall
Mar 31 at 4:33
1
$begingroup$
@JacobKrall good point, or just by varying the feed rate of the work piece against the wheel.
$endgroup$
– uhoh
Mar 31 at 6:39
2
$begingroup$
What are you using to power the wheel? Why don't you use that to power the ship directly?
$endgroup$
– David Richerby
Apr 1 at 11:24
1
$begingroup$
FWIW: youtu.be/SAHmTQWsxeM?t=171Lighter Exhaust Gas == Higher Velocity
(at the same temperature). I'm guessing that would also apply to solids.
$endgroup$
– PEEJWEEJ
Apr 1 at 16:00
|
show 13 more comments
12
$begingroup$
It would need 2 grinding machines for a counter balance.
$endgroup$
– Muze
Mar 30 at 21:58
18
$begingroup$
"The amount of propulsion produced at any one time would be achieved by increasing/decreasing the rotational speed of the grinding wheel." -- More likely, by utilizing a duty cycle of 100% on/off, otherwise you're wasting your fuel by not ejecting it with full force.
$endgroup$
– Jacob Krall
Mar 31 at 4:33
1
$begingroup$
@JacobKrall good point, or just by varying the feed rate of the work piece against the wheel.
$endgroup$
– uhoh
Mar 31 at 6:39
2
$begingroup$
What are you using to power the wheel? Why don't you use that to power the ship directly?
$endgroup$
– David Richerby
Apr 1 at 11:24
1
$begingroup$
FWIW: youtu.be/SAHmTQWsxeM?t=171Lighter Exhaust Gas == Higher Velocity
(at the same temperature). I'm guessing that would also apply to solids.
$endgroup$
– PEEJWEEJ
Apr 1 at 16:00
12
12
$begingroup$
It would need 2 grinding machines for a counter balance.
$endgroup$
– Muze
Mar 30 at 21:58
$begingroup$
It would need 2 grinding machines for a counter balance.
$endgroup$
– Muze
Mar 30 at 21:58
18
18
$begingroup$
"The amount of propulsion produced at any one time would be achieved by increasing/decreasing the rotational speed of the grinding wheel." -- More likely, by utilizing a duty cycle of 100% on/off, otherwise you're wasting your fuel by not ejecting it with full force.
$endgroup$
– Jacob Krall
Mar 31 at 4:33
$begingroup$
"The amount of propulsion produced at any one time would be achieved by increasing/decreasing the rotational speed of the grinding wheel." -- More likely, by utilizing a duty cycle of 100% on/off, otherwise you're wasting your fuel by not ejecting it with full force.
$endgroup$
– Jacob Krall
Mar 31 at 4:33
1
1
$begingroup$
@JacobKrall good point, or just by varying the feed rate of the work piece against the wheel.
$endgroup$
– uhoh
Mar 31 at 6:39
$begingroup$
@JacobKrall good point, or just by varying the feed rate of the work piece against the wheel.
$endgroup$
– uhoh
Mar 31 at 6:39
2
2
$begingroup$
What are you using to power the wheel? Why don't you use that to power the ship directly?
$endgroup$
– David Richerby
Apr 1 at 11:24
$begingroup$
What are you using to power the wheel? Why don't you use that to power the ship directly?
$endgroup$
– David Richerby
Apr 1 at 11:24
1
1
$begingroup$
FWIW: youtu.be/SAHmTQWsxeM?t=171
Lighter Exhaust Gas == Higher Velocity
(at the same temperature). I'm guessing that would also apply to solids.$endgroup$
– PEEJWEEJ
Apr 1 at 16:00
$begingroup$
FWIW: youtu.be/SAHmTQWsxeM?t=171
Lighter Exhaust Gas == Higher Velocity
(at the same temperature). I'm guessing that would also apply to solids.$endgroup$
– PEEJWEEJ
Apr 1 at 16:00
|
show 13 more comments
9 Answers
9
active
oldest
votes
$begingroup$
The main engineering challenge in implementing your proposal is that in order to be competitive with a chemical rocket engine, the grinding wheel must rotate at an extremely high velocity. A typical chemical rocket might have a specific impulse between about 250 and 450 seconds; therefore, the exhaust velocity is about 2500-4500 m/s. In a competitive propulsion system, the edge of the wheel must move at least this fast.
So the real question is: can we build a grinding wheel strong enough to rotate at this velocity without exploding?
For now, the answer is no. The tensile stress at the edge of the wheel is $rho r^2 omega^2 = rho v^2$, where $rho$ is the density, $r$ is the radius, $omega$ is the angular velocity, and $v$ is the velocity. Thus, the velocity at which the edge rotates is limited to $v < sqrt{TS / rho}$, where $TS$ is the ultimate tensile strength of the material the grinding wheel is composed of. Of all materials that we currently know how to produce at macroscopic scales, carbon fiber has the highest ultimate tensile strength per unit mass at about 4000 kN-m/kg. This gives a maximum velocity of 2000 m/s. This is less than the exhaust velocity of even a simple, relatively inefficient chemical rocket.
However, suppose that someone invents a way of mass-producing carbon nanotubes with an ultimate tensile strength of 60 GPa and a density of 1 g/cm$^3$. Then we could theoretically achieve an exhaust velocity of over 7500 m/s, which is excellent. In this scenario, your grinding wheel actually starts to look like a really good idea.
$endgroup$
3
$begingroup$
750 s ISP isn't exactly "excellent", merely good. (There are, after all, practical but politically infeasible designs with close to a hundred times that specific impulse, as well as decent TWR.) Depending on TWR, it may or may not even reduce flight times significantly on important missions like manned Mars trips. (Even ion/MHD drives, with ISPs easily 3-5 times higher than this, need a lot of TWR optimization to make a real difference in flight times.)
$endgroup$
– Nathan Tuggy
Mar 31 at 6:36
1
$begingroup$
@NathanTuggy I think 750 s ISP is excellent for such a simple design. Ion/MHD drives are much more complex, and the grinding wheel should be able to achieve a significantly higher TWR because it can push reaction mass out at a much higher rate.
$endgroup$
– Thorondor
Mar 31 at 6:52
4
$begingroup$
The wheel has to be simultaneously robust and easy to grind. These traits are opposites. A grinding wheel consists of grains of sand that are loosely bound together. If you tried to grind off a carbon composite wheel, you'd lose structural integrity by damaging the carbon fibers, and the wheel would soon disintegrate.
$endgroup$
– Hobbes
Mar 31 at 9:03
9
$begingroup$
@Hobbes The wheel doesn't have to be the source of the propellant - the "stationary" thing in contact with the wheel's rim could be, although the velocity imparted to particles removed from it might be substantially less than the tangential velocity of the wheel rim, so ISP would be smaller.
$endgroup$
– Anthony X
Mar 31 at 18:47
1
$begingroup$
Works, if hardness of the grinder is much higher than that of the ground material. This property of carbon nanotubes is subject to ongoing discussion and research.
$endgroup$
– Everyday Astronaut
Apr 1 at 19:16
|
show 3 more comments
$begingroup$
I don't know if it has ever been considered by anyone.
In my view, this is not a good idea for at least the following reasons:
- It is equivalent to mechanically throwing things retrograde. See this video for an overly simple example. This is obviously not a good way for propulsion, as the specific impulse is very low. Let's talk just about the impulse $$p=mv$$ here, where $m$ is the "reaction mass", i.e. the mass of the material that's being ground, the object being throw backwards, or chemical propellant. $v$ is the velocity of the reaction mass relative to the spacecraft. The velocity $v$ of the sparks is in the order of a few m/s (same velocity as the edge of the grinding wheel. With chemical propellants, it is a few km/s. So, for the same amount $m$ of reaction mass that you carry, classical propulsion gives you a factor of about 1000 more impulse than grinding.
- The produced momentum is kind of stochastic. As can be seen in your graphic, the sparks form a cone instead of a straight line. While the upward and the downward motions statistically cancel each other, their vertical components are a waste. While admittedly this also applies to chemical rocket engines (and ion thrusters?), just throwing some stuff overboard would be more efficient in this respect.
Still, I like this question for thinking out of the box. On a side note, reading the title reminded me of this passage of J.D. Clark's book "Ignition!":
F.A. Tsander in Moscow [...] had suggested that an astronaut might stretch his fuel supply by imitating Phileas Fogg. When a fuel tank was emptied, the astronaut could simply grind it up and add the powdered aluminum thus obtaining to the remaining fuel, whose heating value would be correspondingly enhanced!
I think this was actually tried, but found not to work well because the Aluminium particles take too long to combust, i.e. they continue to burn after they have left the combustion chamber. (Some?) Solid rocket propellants are based on Aluminium, though, but that's different.
Edit: The recent news about dangerous space debris made me think about this question again. Thus, I'm throwing in a third disadvantage of grinding propulsion: it would produce tonnes of untrackable, high velocity particles with stochastic motion characteristics. Sure, one could take some care as to minimize the expected hazard. But with thousands of additional satellites being placed in orbit within the next decade, it might be dangerous to use grinding propulsion in Earth orbit.
$endgroup$
5
$begingroup$
Don't make the velocity "a few m/s". The question doesn't constrain the wheel and bar to any particular composition, there's no reason to choose the worst case to base your answer on. Also, cosine losses are often present in real propulsion systems for various reasons, they are not show-stoppers.
$endgroup$
– uhoh
Mar 31 at 0:22
4
$begingroup$
@uhoh To achieve higher velocities, you have to face greater gee forces on the wheel. They can't move too fast or they break apart. The fastest spinning wheels have to be made out of exotic materials, and they tend not to be used for grinding.
$endgroup$
– Cort Ammon
Mar 31 at 4:06
3
$begingroup$
@uhoh just saying the difference is 3 orders of magnitude. If that can be overcome, we're in business. The thing is that it's smart to exploit chemical energy. Alternatives are possible, but need extensive development, e.g. ion thrusters. I'd like to know some of the reasons for the "cosine losses".
$endgroup$
– Everyday Astronaut
Mar 31 at 5:45
3
$begingroup$
@uhoh What I'm pointing out is that one of the best advantages of this approach is that it might be able to acquire some new reaction mass while in-flight. If some of the materials are exotic, then its harder to acquire that way, and it puts it on par with other approaches which are much easier to work with.
$endgroup$
– Cort Ammon
Mar 31 at 15:31
3
$begingroup$
@uhoh I think the real limit is the tyrany of the rocket equation. You really want high speeds. Now what might work would be a variant. Rather than a grinder, you put solid slugs (rocks?) into a sabot and fire those out of a railgun, preferably finding a way to decelerate and reclaim the sabot afterwards. Railguns can get up to the velocities comparable to chemical fuels, so you'd have your ISP and easy refueling.
$endgroup$
– Cort Ammon
Mar 31 at 17:22
|
show 8 more comments
$begingroup$
The forces involved in spinning a wheel at high speeds are enormous. At 1600 km/h rim speed, the wheels on the Bloodhound SSC experience 50,000 G. Even the slightest imbalance (from, say an abrasive particle coming loose) would be catastrophic.
$endgroup$
$begingroup$
that's a good point and this why I think using a diamond laced grinding wheel would be the most ideal wheel to use, but I know very little about materials engineering so I have to defer this to such an expert.
$endgroup$
– HRIATEXP
Apr 1 at 13:10
add a comment |
$begingroup$
Good for you, for thinking outside the box! Fearlessly pursuing new ideas is where any new breakthrough comes from.
But rocket exhaust moves at thousands of meters per second -- supersonic speeds. Recalling the formula relating acceleration to velocity for circular motion, a=v^2/r. So, given a velocity of 3,000 meters per second and a wheel radius of, say, 1 meter, the acceleration at the rim would be roughly 9,000,000 m/s^2, or 900,000 times Earth gravity. And angular velocity, v=Rw, or 9,000,000 radians per second. I think you would have trouble spinning the wheel up to that kind of speed, and I think you would have trouble finding a wheel material that wouldn't fly apart.
$endgroup$
Some of the information contained in this post requires additional references. Please edit to add citations to reliable sources that support the assertions made here. Unsourced material may be disputed or deleted.
4
$begingroup$
The speed at the rim is the radius times the angular speed. If you cut the radius by a factor of ten the angular speed has to increase by a factor of ten to keep the speed at the rim constant. I believe that brings us up to a hundred million radians per second. I look at those numbers and, well, I think we would probably have to put some work into it yet. It's pretty fast.
$endgroup$
– Greg
Mar 31 at 0:44
$begingroup$
Okay now I'm going to think about this more myself, thanks!
$endgroup$
– uhoh
Mar 31 at 0:49
$begingroup$
Okay it looks like I had it bass ackwards; I'm going to go away think about this more, thanks!
$endgroup$
– uhoh
Mar 31 at 4:19
2
$begingroup$
To put Greg's numbers into context, the rim speed is 10 times bigger, and the acceleration (and therefore stress in the rotor) is 100 times bigger than the current state of the art in aircraft jet engine design. In fact from a mech engineering point of view the size isn't very important - the maximum stress in the rotor depends mainly on the rim speed, not on the diameter and RPM individually.
$endgroup$
– alephzero
Mar 31 at 11:47
$begingroup$
The post notice is for the last bit "I think you would have trouble finding a wheel material that wouldn't fly apart." It would be good if you could provide some context for this instead of appearing to rely entirely on supposition.
$endgroup$
– called2voyage♦
Apr 2 at 12:56
add a comment |
$begingroup$
Propulsion comes from acceleration of a reaction mass.
In this case the grinding wheel serves two purposes:
- separate small bits of the workpiece from bulk at a slow and roughly uniform rate
- accelerate those bits by mechanical friction, in a similar way that a tennis ball launcher uses a matched pair of counter-propagating spinning wheels to shoot a box full of tennis balls one at at time in a controlled direction and speed.
As @Muze points out using a matched pair of counter-propagating spinning wheels would be important in spaceflight as well.
Step 1: requires a large amount of work and there's no reason to do that in space. You can produce the particle on the ground, so your propellant "tank" would be a feed system dispensing pellets or powder. They could be suspended in a fluid for easier feed and to avoid electrostatic clumping.
If you have to produce it in space, for example if you are reusing your lower stage as a reaction mass Horace style (Monty Python reference), then you can grind or otherwise form at a lower speed first with a separate wheel. Particles could be remelted in order to make them spherical, and then size-sorted for the following step.
Step 2: would conceptually be accomplished with a mechanism similar to that of a tennis ball launcher. Two counter-propagating wheels with the particle feed introduced in the small gap between the two wheels' surfaces. The particles would have to be monodipserse, meaning all of a fairly uniform size, and slightly smaller than the gap for good friction. Either the particles or the wheels would have to be elastically compressible enough so that there's a good grip for acceleration, and yet the surfaces should not be readily damaged during the process.
You could also very slightly incline the wheels such that if you had a sorted range of particle sizes they can all be introduced at the appropriate gap width.
However, as @Greg points out and then @ Thorondor demonstrates quantitatively, getting your wheels to spin at mach 10 or faster (for a (mass-)specific impulse or Isp of say 300 or so) is a real materials problem.
One possibility for propellant would be a maximal concentration (essentially HCP) liquid suspension of latex or polymer spheres which can be obtained highly monodisperse with sufficient money. If you don't have a lot of room for propellant, then perhaps metallic or metal oxide or nitride nanospheres can be produced by pyrolysis.
Horiba Scientific
GIF from Tennis ball machine DIY - part 1 a better view of a similar mechanism can be seen in Tennis Tutor Ball Machine mechanics in operation.
$endgroup$
7
$begingroup$
That device is an OSHA finger-trapping-hazard nighmare.
$endgroup$
– Richard
Mar 31 at 8:04
2
$begingroup$
@Richard it's at least a "DIY finger-trapping-hazard nightmare." ;-)
$endgroup$
– uhoh
Mar 31 at 8:07
5
$begingroup$
All reaction mass is good reaction mass, whether it's tennis balls or finger skin...
$endgroup$
– Ingolifs
Mar 31 at 22:36
1
$begingroup$
@Ingolifs Finger skin around a finger that is, and a perhaps a floppy fraying hand following.
$endgroup$
– Peter A. Schneider
Apr 2 at 7:43
add a comment |
$begingroup$
Even if feasible materials-wise, I suspect energy efficiency would be horrible. To spin something fast, where is that (rotational) energy going to come from? If you use an electric motor, you could just modify it to make a plasma drive and use it (more) directly. In your device a lot of that energy gets turned into heat (of the wheel) by friction. Presumably you could recycle that heat to a large extent, but the stuff to do that is already adding another layer of complexity.
$endgroup$
2
$begingroup$
You make a good point. What (might have been) pointed out to me and others in this comment and those that followed though, is that there can be situations in the future where raw material to be used as propellant is not scarce or limited to what's on board, but instead having a means to accelerate the raw material is the limiting factor.
$endgroup$
– uhoh
Mar 31 at 21:57
add a comment |
$begingroup$
The big challenge will be the forces on the outside of the wheel, ripping it apart.
We have to pin the numbers to something, and the easiest number to pin down would be the angular velocity. Zippie style uranium enrichment centrifuges operate around 1,500 revolutions per second, so they make a good benchmark. (Some turbochargers go faster, up to 4,800 revolutions per second, but they are rather small diameters, so easier to manufacture). 1500 rev/sec is about 9500 rad/sec. Since $v=romega$, we can solve for the radius of the wheel, $r=frac{v}{omega}$. Let's target a rather low velocity: 500m/s. Chemical rockets have exhaust velocities in the 2500-4500m/s range, but we can target a lower rate because we can always fuel up later. That pegs us as needing wheels on the order of 50cm in radius.
The exact structure of a Zippie style centrifuge is a closely guarded secret, but Wikipedia gives a notional centrifuge size of 20cm or smaller. This means our wheel is going to be withstanding forces roughly four times that of a nuclear enrichment centrifuge. Now mind you those centrifuges are carefully managed, sealed in vacuum chambers and levitated on magnetic bearings. The forces of accelerating mass with the edge of one of these wheels is going to be far greater. More importantly, they will be off axis, which is always tricky for a centrifuge.
So the material properties we need push the limits of what is used in enrichment centrifuges, just to get to one tenth of the ISP of a rocket. So the real question will be, are there mission plans where 1/10th of a rocket's ISP is useful, but where other technologies are insufficient.
$endgroup$
$begingroup$
Good reference to enrichment centrifuges. Please correct me if I'm wrong, but 500 m/s divided by 9500 rad/s gives 5.3 cm, not 50 cm. If that's right, then it's (in some way) easier to build than an enrichment centrifuge.
$endgroup$
– Everyday Astronaut
Apr 1 at 19:03
add a comment |
$begingroup$
A huge amount of energy would be wasted in the grinding process. Only a tiny fraction would be converted to kinetic energy: the rest would be wasted as heat, plus your grinder would wear down and you would have to have all sorts of complicated mechanisms to keep the thing running.
You could reduce the wear and the energy required to grind off the particles by using a weaker material.
But then you could just decide to not grind the particles off in the first place and throw powder out the back using a spinning wheel without the need to grind it.
But then you can just ionize the powder, eject the particles with an electric field and get rid of the wheel completely. It would be a lot more efficient.
Then you could replace the powder with xenon for more efficiency.
And now you have an ion drive and we already have those.
$endgroup$
1
$begingroup$
How does the heat energy relate to the kinetic energy in such a grinding process?
$endgroup$
– Everyday Astronaut
Apr 2 at 12:49
1
$begingroup$
Good question. I suppose the heat will come from friction which is required to grind off the material. Heat is the internal motion of the atoms in the particles as opposed to their external velocity. The ratio is going to depend on the strength of the material you are grinding, the optimal being no strength (i.e., a powder) which is what I was driving at.
$endgroup$
– rghome
Apr 2 at 14:14
1
$begingroup$
Totally agree with you. This will never have better ISP than ion thrusters. Its only advantage is its obvious refuelability, although I wouldn't rule that out for ion thrusters yet. Still, it would be nice if your qualitative estimate (“huge“) could be backed by some numbers. Also, I don't know about energy efficiency of ion thrusters.
$endgroup$
– Everyday Astronaut
Apr 2 at 18:30
1
$begingroup$
Honestly, for a grinder like in the picture, I think an efficiency of zero would be pretty accurate estimate. They normally consume a couple of hundred watts. If it removed 1 gram a second and ejected it at 100m/s (optimistic figures) that would be 5 watts of energy transferred.
$endgroup$
– rghome
Apr 2 at 21:55
add a comment |
$begingroup$
There are two considerations: one is ISP, which is discussed in several of the answers. The other is energy efficiency - how many joules of input energy end up converted to kinetic energy in the expelled propellant mass.
If you consider a typical rocket, energy efficiency is surprisingly high - IIRC something like 70% of the available chemical energy is converted to kinetic energy of propellant mass ejected along the thrust axis (the remainder is waste heat radiated away or components of propellant velocity perpendicular to the thrust axis).
Using a power plant e.g. nuclear to create electricity to drive a motor involves multiple conversion steps, each of which incurs losses. To begin with, a nuclear reactor itself creates heat which has to be converted to mechanical work (at best about 40% efficient IIRC) which is then converted to electricity (maybe 80%-90% efficient) and then to mechanical (again maybe 80%-90%).
Using a nuclear reaction to heat a propellant which you directly expel (nuclear rocket) gets you back to the same sort of energy efficiency as chemical rockets, but higher ISPs because you can potentially achieve higher temperatures.
$endgroup$
add a comment |
protected by called2voyage♦ Apr 2 at 13:07
Thank you for your interest in this question.
Because it has attracted low-quality or spam answers that had to be removed, posting an answer now requires 10 reputation on this site (the association bonus does not count).
Would you like to answer one of these unanswered questions instead?
9 Answers
9
active
oldest
votes
9 Answers
9
active
oldest
votes
active
oldest
votes
active
oldest
votes
$begingroup$
The main engineering challenge in implementing your proposal is that in order to be competitive with a chemical rocket engine, the grinding wheel must rotate at an extremely high velocity. A typical chemical rocket might have a specific impulse between about 250 and 450 seconds; therefore, the exhaust velocity is about 2500-4500 m/s. In a competitive propulsion system, the edge of the wheel must move at least this fast.
So the real question is: can we build a grinding wheel strong enough to rotate at this velocity without exploding?
For now, the answer is no. The tensile stress at the edge of the wheel is $rho r^2 omega^2 = rho v^2$, where $rho$ is the density, $r$ is the radius, $omega$ is the angular velocity, and $v$ is the velocity. Thus, the velocity at which the edge rotates is limited to $v < sqrt{TS / rho}$, where $TS$ is the ultimate tensile strength of the material the grinding wheel is composed of. Of all materials that we currently know how to produce at macroscopic scales, carbon fiber has the highest ultimate tensile strength per unit mass at about 4000 kN-m/kg. This gives a maximum velocity of 2000 m/s. This is less than the exhaust velocity of even a simple, relatively inefficient chemical rocket.
However, suppose that someone invents a way of mass-producing carbon nanotubes with an ultimate tensile strength of 60 GPa and a density of 1 g/cm$^3$. Then we could theoretically achieve an exhaust velocity of over 7500 m/s, which is excellent. In this scenario, your grinding wheel actually starts to look like a really good idea.
$endgroup$
3
$begingroup$
750 s ISP isn't exactly "excellent", merely good. (There are, after all, practical but politically infeasible designs with close to a hundred times that specific impulse, as well as decent TWR.) Depending on TWR, it may or may not even reduce flight times significantly on important missions like manned Mars trips. (Even ion/MHD drives, with ISPs easily 3-5 times higher than this, need a lot of TWR optimization to make a real difference in flight times.)
$endgroup$
– Nathan Tuggy
Mar 31 at 6:36
1
$begingroup$
@NathanTuggy I think 750 s ISP is excellent for such a simple design. Ion/MHD drives are much more complex, and the grinding wheel should be able to achieve a significantly higher TWR because it can push reaction mass out at a much higher rate.
$endgroup$
– Thorondor
Mar 31 at 6:52
4
$begingroup$
The wheel has to be simultaneously robust and easy to grind. These traits are opposites. A grinding wheel consists of grains of sand that are loosely bound together. If you tried to grind off a carbon composite wheel, you'd lose structural integrity by damaging the carbon fibers, and the wheel would soon disintegrate.
$endgroup$
– Hobbes
Mar 31 at 9:03
9
$begingroup$
@Hobbes The wheel doesn't have to be the source of the propellant - the "stationary" thing in contact with the wheel's rim could be, although the velocity imparted to particles removed from it might be substantially less than the tangential velocity of the wheel rim, so ISP would be smaller.
$endgroup$
– Anthony X
Mar 31 at 18:47
1
$begingroup$
Works, if hardness of the grinder is much higher than that of the ground material. This property of carbon nanotubes is subject to ongoing discussion and research.
$endgroup$
– Everyday Astronaut
Apr 1 at 19:16
|
show 3 more comments
$begingroup$
The main engineering challenge in implementing your proposal is that in order to be competitive with a chemical rocket engine, the grinding wheel must rotate at an extremely high velocity. A typical chemical rocket might have a specific impulse between about 250 and 450 seconds; therefore, the exhaust velocity is about 2500-4500 m/s. In a competitive propulsion system, the edge of the wheel must move at least this fast.
So the real question is: can we build a grinding wheel strong enough to rotate at this velocity without exploding?
For now, the answer is no. The tensile stress at the edge of the wheel is $rho r^2 omega^2 = rho v^2$, where $rho$ is the density, $r$ is the radius, $omega$ is the angular velocity, and $v$ is the velocity. Thus, the velocity at which the edge rotates is limited to $v < sqrt{TS / rho}$, where $TS$ is the ultimate tensile strength of the material the grinding wheel is composed of. Of all materials that we currently know how to produce at macroscopic scales, carbon fiber has the highest ultimate tensile strength per unit mass at about 4000 kN-m/kg. This gives a maximum velocity of 2000 m/s. This is less than the exhaust velocity of even a simple, relatively inefficient chemical rocket.
However, suppose that someone invents a way of mass-producing carbon nanotubes with an ultimate tensile strength of 60 GPa and a density of 1 g/cm$^3$. Then we could theoretically achieve an exhaust velocity of over 7500 m/s, which is excellent. In this scenario, your grinding wheel actually starts to look like a really good idea.
$endgroup$
3
$begingroup$
750 s ISP isn't exactly "excellent", merely good. (There are, after all, practical but politically infeasible designs with close to a hundred times that specific impulse, as well as decent TWR.) Depending on TWR, it may or may not even reduce flight times significantly on important missions like manned Mars trips. (Even ion/MHD drives, with ISPs easily 3-5 times higher than this, need a lot of TWR optimization to make a real difference in flight times.)
$endgroup$
– Nathan Tuggy
Mar 31 at 6:36
1
$begingroup$
@NathanTuggy I think 750 s ISP is excellent for such a simple design. Ion/MHD drives are much more complex, and the grinding wheel should be able to achieve a significantly higher TWR because it can push reaction mass out at a much higher rate.
$endgroup$
– Thorondor
Mar 31 at 6:52
4
$begingroup$
The wheel has to be simultaneously robust and easy to grind. These traits are opposites. A grinding wheel consists of grains of sand that are loosely bound together. If you tried to grind off a carbon composite wheel, you'd lose structural integrity by damaging the carbon fibers, and the wheel would soon disintegrate.
$endgroup$
– Hobbes
Mar 31 at 9:03
9
$begingroup$
@Hobbes The wheel doesn't have to be the source of the propellant - the "stationary" thing in contact with the wheel's rim could be, although the velocity imparted to particles removed from it might be substantially less than the tangential velocity of the wheel rim, so ISP would be smaller.
$endgroup$
– Anthony X
Mar 31 at 18:47
1
$begingroup$
Works, if hardness of the grinder is much higher than that of the ground material. This property of carbon nanotubes is subject to ongoing discussion and research.
$endgroup$
– Everyday Astronaut
Apr 1 at 19:16
|
show 3 more comments
$begingroup$
The main engineering challenge in implementing your proposal is that in order to be competitive with a chemical rocket engine, the grinding wheel must rotate at an extremely high velocity. A typical chemical rocket might have a specific impulse between about 250 and 450 seconds; therefore, the exhaust velocity is about 2500-4500 m/s. In a competitive propulsion system, the edge of the wheel must move at least this fast.
So the real question is: can we build a grinding wheel strong enough to rotate at this velocity without exploding?
For now, the answer is no. The tensile stress at the edge of the wheel is $rho r^2 omega^2 = rho v^2$, where $rho$ is the density, $r$ is the radius, $omega$ is the angular velocity, and $v$ is the velocity. Thus, the velocity at which the edge rotates is limited to $v < sqrt{TS / rho}$, where $TS$ is the ultimate tensile strength of the material the grinding wheel is composed of. Of all materials that we currently know how to produce at macroscopic scales, carbon fiber has the highest ultimate tensile strength per unit mass at about 4000 kN-m/kg. This gives a maximum velocity of 2000 m/s. This is less than the exhaust velocity of even a simple, relatively inefficient chemical rocket.
However, suppose that someone invents a way of mass-producing carbon nanotubes with an ultimate tensile strength of 60 GPa and a density of 1 g/cm$^3$. Then we could theoretically achieve an exhaust velocity of over 7500 m/s, which is excellent. In this scenario, your grinding wheel actually starts to look like a really good idea.
$endgroup$
The main engineering challenge in implementing your proposal is that in order to be competitive with a chemical rocket engine, the grinding wheel must rotate at an extremely high velocity. A typical chemical rocket might have a specific impulse between about 250 and 450 seconds; therefore, the exhaust velocity is about 2500-4500 m/s. In a competitive propulsion system, the edge of the wheel must move at least this fast.
So the real question is: can we build a grinding wheel strong enough to rotate at this velocity without exploding?
For now, the answer is no. The tensile stress at the edge of the wheel is $rho r^2 omega^2 = rho v^2$, where $rho$ is the density, $r$ is the radius, $omega$ is the angular velocity, and $v$ is the velocity. Thus, the velocity at which the edge rotates is limited to $v < sqrt{TS / rho}$, where $TS$ is the ultimate tensile strength of the material the grinding wheel is composed of. Of all materials that we currently know how to produce at macroscopic scales, carbon fiber has the highest ultimate tensile strength per unit mass at about 4000 kN-m/kg. This gives a maximum velocity of 2000 m/s. This is less than the exhaust velocity of even a simple, relatively inefficient chemical rocket.
However, suppose that someone invents a way of mass-producing carbon nanotubes with an ultimate tensile strength of 60 GPa and a density of 1 g/cm$^3$. Then we could theoretically achieve an exhaust velocity of over 7500 m/s, which is excellent. In this scenario, your grinding wheel actually starts to look like a really good idea.
edited Mar 31 at 6:10
answered Mar 31 at 6:00


ThorondorThorondor
44616
44616
3
$begingroup$
750 s ISP isn't exactly "excellent", merely good. (There are, after all, practical but politically infeasible designs with close to a hundred times that specific impulse, as well as decent TWR.) Depending on TWR, it may or may not even reduce flight times significantly on important missions like manned Mars trips. (Even ion/MHD drives, with ISPs easily 3-5 times higher than this, need a lot of TWR optimization to make a real difference in flight times.)
$endgroup$
– Nathan Tuggy
Mar 31 at 6:36
1
$begingroup$
@NathanTuggy I think 750 s ISP is excellent for such a simple design. Ion/MHD drives are much more complex, and the grinding wheel should be able to achieve a significantly higher TWR because it can push reaction mass out at a much higher rate.
$endgroup$
– Thorondor
Mar 31 at 6:52
4
$begingroup$
The wheel has to be simultaneously robust and easy to grind. These traits are opposites. A grinding wheel consists of grains of sand that are loosely bound together. If you tried to grind off a carbon composite wheel, you'd lose structural integrity by damaging the carbon fibers, and the wheel would soon disintegrate.
$endgroup$
– Hobbes
Mar 31 at 9:03
9
$begingroup$
@Hobbes The wheel doesn't have to be the source of the propellant - the "stationary" thing in contact with the wheel's rim could be, although the velocity imparted to particles removed from it might be substantially less than the tangential velocity of the wheel rim, so ISP would be smaller.
$endgroup$
– Anthony X
Mar 31 at 18:47
1
$begingroup$
Works, if hardness of the grinder is much higher than that of the ground material. This property of carbon nanotubes is subject to ongoing discussion and research.
$endgroup$
– Everyday Astronaut
Apr 1 at 19:16
|
show 3 more comments
3
$begingroup$
750 s ISP isn't exactly "excellent", merely good. (There are, after all, practical but politically infeasible designs with close to a hundred times that specific impulse, as well as decent TWR.) Depending on TWR, it may or may not even reduce flight times significantly on important missions like manned Mars trips. (Even ion/MHD drives, with ISPs easily 3-5 times higher than this, need a lot of TWR optimization to make a real difference in flight times.)
$endgroup$
– Nathan Tuggy
Mar 31 at 6:36
1
$begingroup$
@NathanTuggy I think 750 s ISP is excellent for such a simple design. Ion/MHD drives are much more complex, and the grinding wheel should be able to achieve a significantly higher TWR because it can push reaction mass out at a much higher rate.
$endgroup$
– Thorondor
Mar 31 at 6:52
4
$begingroup$
The wheel has to be simultaneously robust and easy to grind. These traits are opposites. A grinding wheel consists of grains of sand that are loosely bound together. If you tried to grind off a carbon composite wheel, you'd lose structural integrity by damaging the carbon fibers, and the wheel would soon disintegrate.
$endgroup$
– Hobbes
Mar 31 at 9:03
9
$begingroup$
@Hobbes The wheel doesn't have to be the source of the propellant - the "stationary" thing in contact with the wheel's rim could be, although the velocity imparted to particles removed from it might be substantially less than the tangential velocity of the wheel rim, so ISP would be smaller.
$endgroup$
– Anthony X
Mar 31 at 18:47
1
$begingroup$
Works, if hardness of the grinder is much higher than that of the ground material. This property of carbon nanotubes is subject to ongoing discussion and research.
$endgroup$
– Everyday Astronaut
Apr 1 at 19:16
3
3
$begingroup$
750 s ISP isn't exactly "excellent", merely good. (There are, after all, practical but politically infeasible designs with close to a hundred times that specific impulse, as well as decent TWR.) Depending on TWR, it may or may not even reduce flight times significantly on important missions like manned Mars trips. (Even ion/MHD drives, with ISPs easily 3-5 times higher than this, need a lot of TWR optimization to make a real difference in flight times.)
$endgroup$
– Nathan Tuggy
Mar 31 at 6:36
$begingroup$
750 s ISP isn't exactly "excellent", merely good. (There are, after all, practical but politically infeasible designs with close to a hundred times that specific impulse, as well as decent TWR.) Depending on TWR, it may or may not even reduce flight times significantly on important missions like manned Mars trips. (Even ion/MHD drives, with ISPs easily 3-5 times higher than this, need a lot of TWR optimization to make a real difference in flight times.)
$endgroup$
– Nathan Tuggy
Mar 31 at 6:36
1
1
$begingroup$
@NathanTuggy I think 750 s ISP is excellent for such a simple design. Ion/MHD drives are much more complex, and the grinding wheel should be able to achieve a significantly higher TWR because it can push reaction mass out at a much higher rate.
$endgroup$
– Thorondor
Mar 31 at 6:52
$begingroup$
@NathanTuggy I think 750 s ISP is excellent for such a simple design. Ion/MHD drives are much more complex, and the grinding wheel should be able to achieve a significantly higher TWR because it can push reaction mass out at a much higher rate.
$endgroup$
– Thorondor
Mar 31 at 6:52
4
4
$begingroup$
The wheel has to be simultaneously robust and easy to grind. These traits are opposites. A grinding wheel consists of grains of sand that are loosely bound together. If you tried to grind off a carbon composite wheel, you'd lose structural integrity by damaging the carbon fibers, and the wheel would soon disintegrate.
$endgroup$
– Hobbes
Mar 31 at 9:03
$begingroup$
The wheel has to be simultaneously robust and easy to grind. These traits are opposites. A grinding wheel consists of grains of sand that are loosely bound together. If you tried to grind off a carbon composite wheel, you'd lose structural integrity by damaging the carbon fibers, and the wheel would soon disintegrate.
$endgroup$
– Hobbes
Mar 31 at 9:03
9
9
$begingroup$
@Hobbes The wheel doesn't have to be the source of the propellant - the "stationary" thing in contact with the wheel's rim could be, although the velocity imparted to particles removed from it might be substantially less than the tangential velocity of the wheel rim, so ISP would be smaller.
$endgroup$
– Anthony X
Mar 31 at 18:47
$begingroup$
@Hobbes The wheel doesn't have to be the source of the propellant - the "stationary" thing in contact with the wheel's rim could be, although the velocity imparted to particles removed from it might be substantially less than the tangential velocity of the wheel rim, so ISP would be smaller.
$endgroup$
– Anthony X
Mar 31 at 18:47
1
1
$begingroup$
Works, if hardness of the grinder is much higher than that of the ground material. This property of carbon nanotubes is subject to ongoing discussion and research.
$endgroup$
– Everyday Astronaut
Apr 1 at 19:16
$begingroup$
Works, if hardness of the grinder is much higher than that of the ground material. This property of carbon nanotubes is subject to ongoing discussion and research.
$endgroup$
– Everyday Astronaut
Apr 1 at 19:16
|
show 3 more comments
$begingroup$
I don't know if it has ever been considered by anyone.
In my view, this is not a good idea for at least the following reasons:
- It is equivalent to mechanically throwing things retrograde. See this video for an overly simple example. This is obviously not a good way for propulsion, as the specific impulse is very low. Let's talk just about the impulse $$p=mv$$ here, where $m$ is the "reaction mass", i.e. the mass of the material that's being ground, the object being throw backwards, or chemical propellant. $v$ is the velocity of the reaction mass relative to the spacecraft. The velocity $v$ of the sparks is in the order of a few m/s (same velocity as the edge of the grinding wheel. With chemical propellants, it is a few km/s. So, for the same amount $m$ of reaction mass that you carry, classical propulsion gives you a factor of about 1000 more impulse than grinding.
- The produced momentum is kind of stochastic. As can be seen in your graphic, the sparks form a cone instead of a straight line. While the upward and the downward motions statistically cancel each other, their vertical components are a waste. While admittedly this also applies to chemical rocket engines (and ion thrusters?), just throwing some stuff overboard would be more efficient in this respect.
Still, I like this question for thinking out of the box. On a side note, reading the title reminded me of this passage of J.D. Clark's book "Ignition!":
F.A. Tsander in Moscow [...] had suggested that an astronaut might stretch his fuel supply by imitating Phileas Fogg. When a fuel tank was emptied, the astronaut could simply grind it up and add the powdered aluminum thus obtaining to the remaining fuel, whose heating value would be correspondingly enhanced!
I think this was actually tried, but found not to work well because the Aluminium particles take too long to combust, i.e. they continue to burn after they have left the combustion chamber. (Some?) Solid rocket propellants are based on Aluminium, though, but that's different.
Edit: The recent news about dangerous space debris made me think about this question again. Thus, I'm throwing in a third disadvantage of grinding propulsion: it would produce tonnes of untrackable, high velocity particles with stochastic motion characteristics. Sure, one could take some care as to minimize the expected hazard. But with thousands of additional satellites being placed in orbit within the next decade, it might be dangerous to use grinding propulsion in Earth orbit.
$endgroup$
5
$begingroup$
Don't make the velocity "a few m/s". The question doesn't constrain the wheel and bar to any particular composition, there's no reason to choose the worst case to base your answer on. Also, cosine losses are often present in real propulsion systems for various reasons, they are not show-stoppers.
$endgroup$
– uhoh
Mar 31 at 0:22
4
$begingroup$
@uhoh To achieve higher velocities, you have to face greater gee forces on the wheel. They can't move too fast or they break apart. The fastest spinning wheels have to be made out of exotic materials, and they tend not to be used for grinding.
$endgroup$
– Cort Ammon
Mar 31 at 4:06
3
$begingroup$
@uhoh just saying the difference is 3 orders of magnitude. If that can be overcome, we're in business. The thing is that it's smart to exploit chemical energy. Alternatives are possible, but need extensive development, e.g. ion thrusters. I'd like to know some of the reasons for the "cosine losses".
$endgroup$
– Everyday Astronaut
Mar 31 at 5:45
3
$begingroup$
@uhoh What I'm pointing out is that one of the best advantages of this approach is that it might be able to acquire some new reaction mass while in-flight. If some of the materials are exotic, then its harder to acquire that way, and it puts it on par with other approaches which are much easier to work with.
$endgroup$
– Cort Ammon
Mar 31 at 15:31
3
$begingroup$
@uhoh I think the real limit is the tyrany of the rocket equation. You really want high speeds. Now what might work would be a variant. Rather than a grinder, you put solid slugs (rocks?) into a sabot and fire those out of a railgun, preferably finding a way to decelerate and reclaim the sabot afterwards. Railguns can get up to the velocities comparable to chemical fuels, so you'd have your ISP and easy refueling.
$endgroup$
– Cort Ammon
Mar 31 at 17:22
|
show 8 more comments
$begingroup$
I don't know if it has ever been considered by anyone.
In my view, this is not a good idea for at least the following reasons:
- It is equivalent to mechanically throwing things retrograde. See this video for an overly simple example. This is obviously not a good way for propulsion, as the specific impulse is very low. Let's talk just about the impulse $$p=mv$$ here, where $m$ is the "reaction mass", i.e. the mass of the material that's being ground, the object being throw backwards, or chemical propellant. $v$ is the velocity of the reaction mass relative to the spacecraft. The velocity $v$ of the sparks is in the order of a few m/s (same velocity as the edge of the grinding wheel. With chemical propellants, it is a few km/s. So, for the same amount $m$ of reaction mass that you carry, classical propulsion gives you a factor of about 1000 more impulse than grinding.
- The produced momentum is kind of stochastic. As can be seen in your graphic, the sparks form a cone instead of a straight line. While the upward and the downward motions statistically cancel each other, their vertical components are a waste. While admittedly this also applies to chemical rocket engines (and ion thrusters?), just throwing some stuff overboard would be more efficient in this respect.
Still, I like this question for thinking out of the box. On a side note, reading the title reminded me of this passage of J.D. Clark's book "Ignition!":
F.A. Tsander in Moscow [...] had suggested that an astronaut might stretch his fuel supply by imitating Phileas Fogg. When a fuel tank was emptied, the astronaut could simply grind it up and add the powdered aluminum thus obtaining to the remaining fuel, whose heating value would be correspondingly enhanced!
I think this was actually tried, but found not to work well because the Aluminium particles take too long to combust, i.e. they continue to burn after they have left the combustion chamber. (Some?) Solid rocket propellants are based on Aluminium, though, but that's different.
Edit: The recent news about dangerous space debris made me think about this question again. Thus, I'm throwing in a third disadvantage of grinding propulsion: it would produce tonnes of untrackable, high velocity particles with stochastic motion characteristics. Sure, one could take some care as to minimize the expected hazard. But with thousands of additional satellites being placed in orbit within the next decade, it might be dangerous to use grinding propulsion in Earth orbit.
$endgroup$
5
$begingroup$
Don't make the velocity "a few m/s". The question doesn't constrain the wheel and bar to any particular composition, there's no reason to choose the worst case to base your answer on. Also, cosine losses are often present in real propulsion systems for various reasons, they are not show-stoppers.
$endgroup$
– uhoh
Mar 31 at 0:22
4
$begingroup$
@uhoh To achieve higher velocities, you have to face greater gee forces on the wheel. They can't move too fast or they break apart. The fastest spinning wheels have to be made out of exotic materials, and they tend not to be used for grinding.
$endgroup$
– Cort Ammon
Mar 31 at 4:06
3
$begingroup$
@uhoh just saying the difference is 3 orders of magnitude. If that can be overcome, we're in business. The thing is that it's smart to exploit chemical energy. Alternatives are possible, but need extensive development, e.g. ion thrusters. I'd like to know some of the reasons for the "cosine losses".
$endgroup$
– Everyday Astronaut
Mar 31 at 5:45
3
$begingroup$
@uhoh What I'm pointing out is that one of the best advantages of this approach is that it might be able to acquire some new reaction mass while in-flight. If some of the materials are exotic, then its harder to acquire that way, and it puts it on par with other approaches which are much easier to work with.
$endgroup$
– Cort Ammon
Mar 31 at 15:31
3
$begingroup$
@uhoh I think the real limit is the tyrany of the rocket equation. You really want high speeds. Now what might work would be a variant. Rather than a grinder, you put solid slugs (rocks?) into a sabot and fire those out of a railgun, preferably finding a way to decelerate and reclaim the sabot afterwards. Railguns can get up to the velocities comparable to chemical fuels, so you'd have your ISP and easy refueling.
$endgroup$
– Cort Ammon
Mar 31 at 17:22
|
show 8 more comments
$begingroup$
I don't know if it has ever been considered by anyone.
In my view, this is not a good idea for at least the following reasons:
- It is equivalent to mechanically throwing things retrograde. See this video for an overly simple example. This is obviously not a good way for propulsion, as the specific impulse is very low. Let's talk just about the impulse $$p=mv$$ here, where $m$ is the "reaction mass", i.e. the mass of the material that's being ground, the object being throw backwards, or chemical propellant. $v$ is the velocity of the reaction mass relative to the spacecraft. The velocity $v$ of the sparks is in the order of a few m/s (same velocity as the edge of the grinding wheel. With chemical propellants, it is a few km/s. So, for the same amount $m$ of reaction mass that you carry, classical propulsion gives you a factor of about 1000 more impulse than grinding.
- The produced momentum is kind of stochastic. As can be seen in your graphic, the sparks form a cone instead of a straight line. While the upward and the downward motions statistically cancel each other, their vertical components are a waste. While admittedly this also applies to chemical rocket engines (and ion thrusters?), just throwing some stuff overboard would be more efficient in this respect.
Still, I like this question for thinking out of the box. On a side note, reading the title reminded me of this passage of J.D. Clark's book "Ignition!":
F.A. Tsander in Moscow [...] had suggested that an astronaut might stretch his fuel supply by imitating Phileas Fogg. When a fuel tank was emptied, the astronaut could simply grind it up and add the powdered aluminum thus obtaining to the remaining fuel, whose heating value would be correspondingly enhanced!
I think this was actually tried, but found not to work well because the Aluminium particles take too long to combust, i.e. they continue to burn after they have left the combustion chamber. (Some?) Solid rocket propellants are based on Aluminium, though, but that's different.
Edit: The recent news about dangerous space debris made me think about this question again. Thus, I'm throwing in a third disadvantage of grinding propulsion: it would produce tonnes of untrackable, high velocity particles with stochastic motion characteristics. Sure, one could take some care as to minimize the expected hazard. But with thousands of additional satellites being placed in orbit within the next decade, it might be dangerous to use grinding propulsion in Earth orbit.
$endgroup$
I don't know if it has ever been considered by anyone.
In my view, this is not a good idea for at least the following reasons:
- It is equivalent to mechanically throwing things retrograde. See this video for an overly simple example. This is obviously not a good way for propulsion, as the specific impulse is very low. Let's talk just about the impulse $$p=mv$$ here, where $m$ is the "reaction mass", i.e. the mass of the material that's being ground, the object being throw backwards, or chemical propellant. $v$ is the velocity of the reaction mass relative to the spacecraft. The velocity $v$ of the sparks is in the order of a few m/s (same velocity as the edge of the grinding wheel. With chemical propellants, it is a few km/s. So, for the same amount $m$ of reaction mass that you carry, classical propulsion gives you a factor of about 1000 more impulse than grinding.
- The produced momentum is kind of stochastic. As can be seen in your graphic, the sparks form a cone instead of a straight line. While the upward and the downward motions statistically cancel each other, their vertical components are a waste. While admittedly this also applies to chemical rocket engines (and ion thrusters?), just throwing some stuff overboard would be more efficient in this respect.
Still, I like this question for thinking out of the box. On a side note, reading the title reminded me of this passage of J.D. Clark's book "Ignition!":
F.A. Tsander in Moscow [...] had suggested that an astronaut might stretch his fuel supply by imitating Phileas Fogg. When a fuel tank was emptied, the astronaut could simply grind it up and add the powdered aluminum thus obtaining to the remaining fuel, whose heating value would be correspondingly enhanced!
I think this was actually tried, but found not to work well because the Aluminium particles take too long to combust, i.e. they continue to burn after they have left the combustion chamber. (Some?) Solid rocket propellants are based on Aluminium, though, but that's different.
Edit: The recent news about dangerous space debris made me think about this question again. Thus, I'm throwing in a third disadvantage of grinding propulsion: it would produce tonnes of untrackable, high velocity particles with stochastic motion characteristics. Sure, one could take some care as to minimize the expected hazard. But with thousands of additional satellites being placed in orbit within the next decade, it might be dangerous to use grinding propulsion in Earth orbit.
edited Apr 2 at 21:29
answered Mar 30 at 22:29
Everyday AstronautEveryday Astronaut
2,384835
2,384835
5
$begingroup$
Don't make the velocity "a few m/s". The question doesn't constrain the wheel and bar to any particular composition, there's no reason to choose the worst case to base your answer on. Also, cosine losses are often present in real propulsion systems for various reasons, they are not show-stoppers.
$endgroup$
– uhoh
Mar 31 at 0:22
4
$begingroup$
@uhoh To achieve higher velocities, you have to face greater gee forces on the wheel. They can't move too fast or they break apart. The fastest spinning wheels have to be made out of exotic materials, and they tend not to be used for grinding.
$endgroup$
– Cort Ammon
Mar 31 at 4:06
3
$begingroup$
@uhoh just saying the difference is 3 orders of magnitude. If that can be overcome, we're in business. The thing is that it's smart to exploit chemical energy. Alternatives are possible, but need extensive development, e.g. ion thrusters. I'd like to know some of the reasons for the "cosine losses".
$endgroup$
– Everyday Astronaut
Mar 31 at 5:45
3
$begingroup$
@uhoh What I'm pointing out is that one of the best advantages of this approach is that it might be able to acquire some new reaction mass while in-flight. If some of the materials are exotic, then its harder to acquire that way, and it puts it on par with other approaches which are much easier to work with.
$endgroup$
– Cort Ammon
Mar 31 at 15:31
3
$begingroup$
@uhoh I think the real limit is the tyrany of the rocket equation. You really want high speeds. Now what might work would be a variant. Rather than a grinder, you put solid slugs (rocks?) into a sabot and fire those out of a railgun, preferably finding a way to decelerate and reclaim the sabot afterwards. Railguns can get up to the velocities comparable to chemical fuels, so you'd have your ISP and easy refueling.
$endgroup$
– Cort Ammon
Mar 31 at 17:22
|
show 8 more comments
5
$begingroup$
Don't make the velocity "a few m/s". The question doesn't constrain the wheel and bar to any particular composition, there's no reason to choose the worst case to base your answer on. Also, cosine losses are often present in real propulsion systems for various reasons, they are not show-stoppers.
$endgroup$
– uhoh
Mar 31 at 0:22
4
$begingroup$
@uhoh To achieve higher velocities, you have to face greater gee forces on the wheel. They can't move too fast or they break apart. The fastest spinning wheels have to be made out of exotic materials, and they tend not to be used for grinding.
$endgroup$
– Cort Ammon
Mar 31 at 4:06
3
$begingroup$
@uhoh just saying the difference is 3 orders of magnitude. If that can be overcome, we're in business. The thing is that it's smart to exploit chemical energy. Alternatives are possible, but need extensive development, e.g. ion thrusters. I'd like to know some of the reasons for the "cosine losses".
$endgroup$
– Everyday Astronaut
Mar 31 at 5:45
3
$begingroup$
@uhoh What I'm pointing out is that one of the best advantages of this approach is that it might be able to acquire some new reaction mass while in-flight. If some of the materials are exotic, then its harder to acquire that way, and it puts it on par with other approaches which are much easier to work with.
$endgroup$
– Cort Ammon
Mar 31 at 15:31
3
$begingroup$
@uhoh I think the real limit is the tyrany of the rocket equation. You really want high speeds. Now what might work would be a variant. Rather than a grinder, you put solid slugs (rocks?) into a sabot and fire those out of a railgun, preferably finding a way to decelerate and reclaim the sabot afterwards. Railguns can get up to the velocities comparable to chemical fuels, so you'd have your ISP and easy refueling.
$endgroup$
– Cort Ammon
Mar 31 at 17:22
5
5
$begingroup$
Don't make the velocity "a few m/s". The question doesn't constrain the wheel and bar to any particular composition, there's no reason to choose the worst case to base your answer on. Also, cosine losses are often present in real propulsion systems for various reasons, they are not show-stoppers.
$endgroup$
– uhoh
Mar 31 at 0:22
$begingroup$
Don't make the velocity "a few m/s". The question doesn't constrain the wheel and bar to any particular composition, there's no reason to choose the worst case to base your answer on. Also, cosine losses are often present in real propulsion systems for various reasons, they are not show-stoppers.
$endgroup$
– uhoh
Mar 31 at 0:22
4
4
$begingroup$
@uhoh To achieve higher velocities, you have to face greater gee forces on the wheel. They can't move too fast or they break apart. The fastest spinning wheels have to be made out of exotic materials, and they tend not to be used for grinding.
$endgroup$
– Cort Ammon
Mar 31 at 4:06
$begingroup$
@uhoh To achieve higher velocities, you have to face greater gee forces on the wheel. They can't move too fast or they break apart. The fastest spinning wheels have to be made out of exotic materials, and they tend not to be used for grinding.
$endgroup$
– Cort Ammon
Mar 31 at 4:06
3
3
$begingroup$
@uhoh just saying the difference is 3 orders of magnitude. If that can be overcome, we're in business. The thing is that it's smart to exploit chemical energy. Alternatives are possible, but need extensive development, e.g. ion thrusters. I'd like to know some of the reasons for the "cosine losses".
$endgroup$
– Everyday Astronaut
Mar 31 at 5:45
$begingroup$
@uhoh just saying the difference is 3 orders of magnitude. If that can be overcome, we're in business. The thing is that it's smart to exploit chemical energy. Alternatives are possible, but need extensive development, e.g. ion thrusters. I'd like to know some of the reasons for the "cosine losses".
$endgroup$
– Everyday Astronaut
Mar 31 at 5:45
3
3
$begingroup$
@uhoh What I'm pointing out is that one of the best advantages of this approach is that it might be able to acquire some new reaction mass while in-flight. If some of the materials are exotic, then its harder to acquire that way, and it puts it on par with other approaches which are much easier to work with.
$endgroup$
– Cort Ammon
Mar 31 at 15:31
$begingroup$
@uhoh What I'm pointing out is that one of the best advantages of this approach is that it might be able to acquire some new reaction mass while in-flight. If some of the materials are exotic, then its harder to acquire that way, and it puts it on par with other approaches which are much easier to work with.
$endgroup$
– Cort Ammon
Mar 31 at 15:31
3
3
$begingroup$
@uhoh I think the real limit is the tyrany of the rocket equation. You really want high speeds. Now what might work would be a variant. Rather than a grinder, you put solid slugs (rocks?) into a sabot and fire those out of a railgun, preferably finding a way to decelerate and reclaim the sabot afterwards. Railguns can get up to the velocities comparable to chemical fuels, so you'd have your ISP and easy refueling.
$endgroup$
– Cort Ammon
Mar 31 at 17:22
$begingroup$
@uhoh I think the real limit is the tyrany of the rocket equation. You really want high speeds. Now what might work would be a variant. Rather than a grinder, you put solid slugs (rocks?) into a sabot and fire those out of a railgun, preferably finding a way to decelerate and reclaim the sabot afterwards. Railguns can get up to the velocities comparable to chemical fuels, so you'd have your ISP and easy refueling.
$endgroup$
– Cort Ammon
Mar 31 at 17:22
|
show 8 more comments
$begingroup$
The forces involved in spinning a wheel at high speeds are enormous. At 1600 km/h rim speed, the wheels on the Bloodhound SSC experience 50,000 G. Even the slightest imbalance (from, say an abrasive particle coming loose) would be catastrophic.
$endgroup$
$begingroup$
that's a good point and this why I think using a diamond laced grinding wheel would be the most ideal wheel to use, but I know very little about materials engineering so I have to defer this to such an expert.
$endgroup$
– HRIATEXP
Apr 1 at 13:10
add a comment |
$begingroup$
The forces involved in spinning a wheel at high speeds are enormous. At 1600 km/h rim speed, the wheels on the Bloodhound SSC experience 50,000 G. Even the slightest imbalance (from, say an abrasive particle coming loose) would be catastrophic.
$endgroup$
$begingroup$
that's a good point and this why I think using a diamond laced grinding wheel would be the most ideal wheel to use, but I know very little about materials engineering so I have to defer this to such an expert.
$endgroup$
– HRIATEXP
Apr 1 at 13:10
add a comment |
$begingroup$
The forces involved in spinning a wheel at high speeds are enormous. At 1600 km/h rim speed, the wheels on the Bloodhound SSC experience 50,000 G. Even the slightest imbalance (from, say an abrasive particle coming loose) would be catastrophic.
$endgroup$
The forces involved in spinning a wheel at high speeds are enormous. At 1600 km/h rim speed, the wheels on the Bloodhound SSC experience 50,000 G. Even the slightest imbalance (from, say an abrasive particle coming loose) would be catastrophic.
answered Apr 1 at 10:05
HobbesHobbes
95.9k2272426
95.9k2272426
$begingroup$
that's a good point and this why I think using a diamond laced grinding wheel would be the most ideal wheel to use, but I know very little about materials engineering so I have to defer this to such an expert.
$endgroup$
– HRIATEXP
Apr 1 at 13:10
add a comment |
$begingroup$
that's a good point and this why I think using a diamond laced grinding wheel would be the most ideal wheel to use, but I know very little about materials engineering so I have to defer this to such an expert.
$endgroup$
– HRIATEXP
Apr 1 at 13:10
$begingroup$
that's a good point and this why I think using a diamond laced grinding wheel would be the most ideal wheel to use, but I know very little about materials engineering so I have to defer this to such an expert.
$endgroup$
– HRIATEXP
Apr 1 at 13:10
$begingroup$
that's a good point and this why I think using a diamond laced grinding wheel would be the most ideal wheel to use, but I know very little about materials engineering so I have to defer this to such an expert.
$endgroup$
– HRIATEXP
Apr 1 at 13:10
add a comment |
$begingroup$
Good for you, for thinking outside the box! Fearlessly pursuing new ideas is where any new breakthrough comes from.
But rocket exhaust moves at thousands of meters per second -- supersonic speeds. Recalling the formula relating acceleration to velocity for circular motion, a=v^2/r. So, given a velocity of 3,000 meters per second and a wheel radius of, say, 1 meter, the acceleration at the rim would be roughly 9,000,000 m/s^2, or 900,000 times Earth gravity. And angular velocity, v=Rw, or 9,000,000 radians per second. I think you would have trouble spinning the wheel up to that kind of speed, and I think you would have trouble finding a wheel material that wouldn't fly apart.
$endgroup$
Some of the information contained in this post requires additional references. Please edit to add citations to reliable sources that support the assertions made here. Unsourced material may be disputed or deleted.
4
$begingroup$
The speed at the rim is the radius times the angular speed. If you cut the radius by a factor of ten the angular speed has to increase by a factor of ten to keep the speed at the rim constant. I believe that brings us up to a hundred million radians per second. I look at those numbers and, well, I think we would probably have to put some work into it yet. It's pretty fast.
$endgroup$
– Greg
Mar 31 at 0:44
$begingroup$
Okay now I'm going to think about this more myself, thanks!
$endgroup$
– uhoh
Mar 31 at 0:49
$begingroup$
Okay it looks like I had it bass ackwards; I'm going to go away think about this more, thanks!
$endgroup$
– uhoh
Mar 31 at 4:19
2
$begingroup$
To put Greg's numbers into context, the rim speed is 10 times bigger, and the acceleration (and therefore stress in the rotor) is 100 times bigger than the current state of the art in aircraft jet engine design. In fact from a mech engineering point of view the size isn't very important - the maximum stress in the rotor depends mainly on the rim speed, not on the diameter and RPM individually.
$endgroup$
– alephzero
Mar 31 at 11:47
$begingroup$
The post notice is for the last bit "I think you would have trouble finding a wheel material that wouldn't fly apart." It would be good if you could provide some context for this instead of appearing to rely entirely on supposition.
$endgroup$
– called2voyage♦
Apr 2 at 12:56
add a comment |
$begingroup$
Good for you, for thinking outside the box! Fearlessly pursuing new ideas is where any new breakthrough comes from.
But rocket exhaust moves at thousands of meters per second -- supersonic speeds. Recalling the formula relating acceleration to velocity for circular motion, a=v^2/r. So, given a velocity of 3,000 meters per second and a wheel radius of, say, 1 meter, the acceleration at the rim would be roughly 9,000,000 m/s^2, or 900,000 times Earth gravity. And angular velocity, v=Rw, or 9,000,000 radians per second. I think you would have trouble spinning the wheel up to that kind of speed, and I think you would have trouble finding a wheel material that wouldn't fly apart.
$endgroup$
Some of the information contained in this post requires additional references. Please edit to add citations to reliable sources that support the assertions made here. Unsourced material may be disputed or deleted.
4
$begingroup$
The speed at the rim is the radius times the angular speed. If you cut the radius by a factor of ten the angular speed has to increase by a factor of ten to keep the speed at the rim constant. I believe that brings us up to a hundred million radians per second. I look at those numbers and, well, I think we would probably have to put some work into it yet. It's pretty fast.
$endgroup$
– Greg
Mar 31 at 0:44
$begingroup$
Okay now I'm going to think about this more myself, thanks!
$endgroup$
– uhoh
Mar 31 at 0:49
$begingroup$
Okay it looks like I had it bass ackwards; I'm going to go away think about this more, thanks!
$endgroup$
– uhoh
Mar 31 at 4:19
2
$begingroup$
To put Greg's numbers into context, the rim speed is 10 times bigger, and the acceleration (and therefore stress in the rotor) is 100 times bigger than the current state of the art in aircraft jet engine design. In fact from a mech engineering point of view the size isn't very important - the maximum stress in the rotor depends mainly on the rim speed, not on the diameter and RPM individually.
$endgroup$
– alephzero
Mar 31 at 11:47
$begingroup$
The post notice is for the last bit "I think you would have trouble finding a wheel material that wouldn't fly apart." It would be good if you could provide some context for this instead of appearing to rely entirely on supposition.
$endgroup$
– called2voyage♦
Apr 2 at 12:56
add a comment |
$begingroup$
Good for you, for thinking outside the box! Fearlessly pursuing new ideas is where any new breakthrough comes from.
But rocket exhaust moves at thousands of meters per second -- supersonic speeds. Recalling the formula relating acceleration to velocity for circular motion, a=v^2/r. So, given a velocity of 3,000 meters per second and a wheel radius of, say, 1 meter, the acceleration at the rim would be roughly 9,000,000 m/s^2, or 900,000 times Earth gravity. And angular velocity, v=Rw, or 9,000,000 radians per second. I think you would have trouble spinning the wheel up to that kind of speed, and I think you would have trouble finding a wheel material that wouldn't fly apart.
$endgroup$
Good for you, for thinking outside the box! Fearlessly pursuing new ideas is where any new breakthrough comes from.
But rocket exhaust moves at thousands of meters per second -- supersonic speeds. Recalling the formula relating acceleration to velocity for circular motion, a=v^2/r. So, given a velocity of 3,000 meters per second and a wheel radius of, say, 1 meter, the acceleration at the rim would be roughly 9,000,000 m/s^2, or 900,000 times Earth gravity. And angular velocity, v=Rw, or 9,000,000 radians per second. I think you would have trouble spinning the wheel up to that kind of speed, and I think you would have trouble finding a wheel material that wouldn't fly apart.
answered Mar 30 at 22:51
GregGreg
98939
98939
Some of the information contained in this post requires additional references. Please edit to add citations to reliable sources that support the assertions made here. Unsourced material may be disputed or deleted.
Some of the information contained in this post requires additional references. Please edit to add citations to reliable sources that support the assertions made here. Unsourced material may be disputed or deleted.
4
$begingroup$
The speed at the rim is the radius times the angular speed. If you cut the radius by a factor of ten the angular speed has to increase by a factor of ten to keep the speed at the rim constant. I believe that brings us up to a hundred million radians per second. I look at those numbers and, well, I think we would probably have to put some work into it yet. It's pretty fast.
$endgroup$
– Greg
Mar 31 at 0:44
$begingroup$
Okay now I'm going to think about this more myself, thanks!
$endgroup$
– uhoh
Mar 31 at 0:49
$begingroup$
Okay it looks like I had it bass ackwards; I'm going to go away think about this more, thanks!
$endgroup$
– uhoh
Mar 31 at 4:19
2
$begingroup$
To put Greg's numbers into context, the rim speed is 10 times bigger, and the acceleration (and therefore stress in the rotor) is 100 times bigger than the current state of the art in aircraft jet engine design. In fact from a mech engineering point of view the size isn't very important - the maximum stress in the rotor depends mainly on the rim speed, not on the diameter and RPM individually.
$endgroup$
– alephzero
Mar 31 at 11:47
$begingroup$
The post notice is for the last bit "I think you would have trouble finding a wheel material that wouldn't fly apart." It would be good if you could provide some context for this instead of appearing to rely entirely on supposition.
$endgroup$
– called2voyage♦
Apr 2 at 12:56
add a comment |
4
$begingroup$
The speed at the rim is the radius times the angular speed. If you cut the radius by a factor of ten the angular speed has to increase by a factor of ten to keep the speed at the rim constant. I believe that brings us up to a hundred million radians per second. I look at those numbers and, well, I think we would probably have to put some work into it yet. It's pretty fast.
$endgroup$
– Greg
Mar 31 at 0:44
$begingroup$
Okay now I'm going to think about this more myself, thanks!
$endgroup$
– uhoh
Mar 31 at 0:49
$begingroup$
Okay it looks like I had it bass ackwards; I'm going to go away think about this more, thanks!
$endgroup$
– uhoh
Mar 31 at 4:19
2
$begingroup$
To put Greg's numbers into context, the rim speed is 10 times bigger, and the acceleration (and therefore stress in the rotor) is 100 times bigger than the current state of the art in aircraft jet engine design. In fact from a mech engineering point of view the size isn't very important - the maximum stress in the rotor depends mainly on the rim speed, not on the diameter and RPM individually.
$endgroup$
– alephzero
Mar 31 at 11:47
$begingroup$
The post notice is for the last bit "I think you would have trouble finding a wheel material that wouldn't fly apart." It would be good if you could provide some context for this instead of appearing to rely entirely on supposition.
$endgroup$
– called2voyage♦
Apr 2 at 12:56
4
4
$begingroup$
The speed at the rim is the radius times the angular speed. If you cut the radius by a factor of ten the angular speed has to increase by a factor of ten to keep the speed at the rim constant. I believe that brings us up to a hundred million radians per second. I look at those numbers and, well, I think we would probably have to put some work into it yet. It's pretty fast.
$endgroup$
– Greg
Mar 31 at 0:44
$begingroup$
The speed at the rim is the radius times the angular speed. If you cut the radius by a factor of ten the angular speed has to increase by a factor of ten to keep the speed at the rim constant. I believe that brings us up to a hundred million radians per second. I look at those numbers and, well, I think we would probably have to put some work into it yet. It's pretty fast.
$endgroup$
– Greg
Mar 31 at 0:44
$begingroup$
Okay now I'm going to think about this more myself, thanks!
$endgroup$
– uhoh
Mar 31 at 0:49
$begingroup$
Okay now I'm going to think about this more myself, thanks!
$endgroup$
– uhoh
Mar 31 at 0:49
$begingroup$
Okay it looks like I had it bass ackwards; I'm going to go away think about this more, thanks!
$endgroup$
– uhoh
Mar 31 at 4:19
$begingroup$
Okay it looks like I had it bass ackwards; I'm going to go away think about this more, thanks!
$endgroup$
– uhoh
Mar 31 at 4:19
2
2
$begingroup$
To put Greg's numbers into context, the rim speed is 10 times bigger, and the acceleration (and therefore stress in the rotor) is 100 times bigger than the current state of the art in aircraft jet engine design. In fact from a mech engineering point of view the size isn't very important - the maximum stress in the rotor depends mainly on the rim speed, not on the diameter and RPM individually.
$endgroup$
– alephzero
Mar 31 at 11:47
$begingroup$
To put Greg's numbers into context, the rim speed is 10 times bigger, and the acceleration (and therefore stress in the rotor) is 100 times bigger than the current state of the art in aircraft jet engine design. In fact from a mech engineering point of view the size isn't very important - the maximum stress in the rotor depends mainly on the rim speed, not on the diameter and RPM individually.
$endgroup$
– alephzero
Mar 31 at 11:47
$begingroup$
The post notice is for the last bit "I think you would have trouble finding a wheel material that wouldn't fly apart." It would be good if you could provide some context for this instead of appearing to rely entirely on supposition.
$endgroup$
– called2voyage♦
Apr 2 at 12:56
$begingroup$
The post notice is for the last bit "I think you would have trouble finding a wheel material that wouldn't fly apart." It would be good if you could provide some context for this instead of appearing to rely entirely on supposition.
$endgroup$
– called2voyage♦
Apr 2 at 12:56
add a comment |
$begingroup$
Propulsion comes from acceleration of a reaction mass.
In this case the grinding wheel serves two purposes:
- separate small bits of the workpiece from bulk at a slow and roughly uniform rate
- accelerate those bits by mechanical friction, in a similar way that a tennis ball launcher uses a matched pair of counter-propagating spinning wheels to shoot a box full of tennis balls one at at time in a controlled direction and speed.
As @Muze points out using a matched pair of counter-propagating spinning wheels would be important in spaceflight as well.
Step 1: requires a large amount of work and there's no reason to do that in space. You can produce the particle on the ground, so your propellant "tank" would be a feed system dispensing pellets or powder. They could be suspended in a fluid for easier feed and to avoid electrostatic clumping.
If you have to produce it in space, for example if you are reusing your lower stage as a reaction mass Horace style (Monty Python reference), then you can grind or otherwise form at a lower speed first with a separate wheel. Particles could be remelted in order to make them spherical, and then size-sorted for the following step.
Step 2: would conceptually be accomplished with a mechanism similar to that of a tennis ball launcher. Two counter-propagating wheels with the particle feed introduced in the small gap between the two wheels' surfaces. The particles would have to be monodipserse, meaning all of a fairly uniform size, and slightly smaller than the gap for good friction. Either the particles or the wheels would have to be elastically compressible enough so that there's a good grip for acceleration, and yet the surfaces should not be readily damaged during the process.
You could also very slightly incline the wheels such that if you had a sorted range of particle sizes they can all be introduced at the appropriate gap width.
However, as @Greg points out and then @ Thorondor demonstrates quantitatively, getting your wheels to spin at mach 10 or faster (for a (mass-)specific impulse or Isp of say 300 or so) is a real materials problem.
One possibility for propellant would be a maximal concentration (essentially HCP) liquid suspension of latex or polymer spheres which can be obtained highly monodisperse with sufficient money. If you don't have a lot of room for propellant, then perhaps metallic or metal oxide or nitride nanospheres can be produced by pyrolysis.
Horiba Scientific
GIF from Tennis ball machine DIY - part 1 a better view of a similar mechanism can be seen in Tennis Tutor Ball Machine mechanics in operation.
$endgroup$
7
$begingroup$
That device is an OSHA finger-trapping-hazard nighmare.
$endgroup$
– Richard
Mar 31 at 8:04
2
$begingroup$
@Richard it's at least a "DIY finger-trapping-hazard nightmare." ;-)
$endgroup$
– uhoh
Mar 31 at 8:07
5
$begingroup$
All reaction mass is good reaction mass, whether it's tennis balls or finger skin...
$endgroup$
– Ingolifs
Mar 31 at 22:36
1
$begingroup$
@Ingolifs Finger skin around a finger that is, and a perhaps a floppy fraying hand following.
$endgroup$
– Peter A. Schneider
Apr 2 at 7:43
add a comment |
$begingroup$
Propulsion comes from acceleration of a reaction mass.
In this case the grinding wheel serves two purposes:
- separate small bits of the workpiece from bulk at a slow and roughly uniform rate
- accelerate those bits by mechanical friction, in a similar way that a tennis ball launcher uses a matched pair of counter-propagating spinning wheels to shoot a box full of tennis balls one at at time in a controlled direction and speed.
As @Muze points out using a matched pair of counter-propagating spinning wheels would be important in spaceflight as well.
Step 1: requires a large amount of work and there's no reason to do that in space. You can produce the particle on the ground, so your propellant "tank" would be a feed system dispensing pellets or powder. They could be suspended in a fluid for easier feed and to avoid electrostatic clumping.
If you have to produce it in space, for example if you are reusing your lower stage as a reaction mass Horace style (Monty Python reference), then you can grind or otherwise form at a lower speed first with a separate wheel. Particles could be remelted in order to make them spherical, and then size-sorted for the following step.
Step 2: would conceptually be accomplished with a mechanism similar to that of a tennis ball launcher. Two counter-propagating wheels with the particle feed introduced in the small gap between the two wheels' surfaces. The particles would have to be monodipserse, meaning all of a fairly uniform size, and slightly smaller than the gap for good friction. Either the particles or the wheels would have to be elastically compressible enough so that there's a good grip for acceleration, and yet the surfaces should not be readily damaged during the process.
You could also very slightly incline the wheels such that if you had a sorted range of particle sizes they can all be introduced at the appropriate gap width.
However, as @Greg points out and then @ Thorondor demonstrates quantitatively, getting your wheels to spin at mach 10 or faster (for a (mass-)specific impulse or Isp of say 300 or so) is a real materials problem.
One possibility for propellant would be a maximal concentration (essentially HCP) liquid suspension of latex or polymer spheres which can be obtained highly monodisperse with sufficient money. If you don't have a lot of room for propellant, then perhaps metallic or metal oxide or nitride nanospheres can be produced by pyrolysis.
Horiba Scientific
GIF from Tennis ball machine DIY - part 1 a better view of a similar mechanism can be seen in Tennis Tutor Ball Machine mechanics in operation.
$endgroup$
7
$begingroup$
That device is an OSHA finger-trapping-hazard nighmare.
$endgroup$
– Richard
Mar 31 at 8:04
2
$begingroup$
@Richard it's at least a "DIY finger-trapping-hazard nightmare." ;-)
$endgroup$
– uhoh
Mar 31 at 8:07
5
$begingroup$
All reaction mass is good reaction mass, whether it's tennis balls or finger skin...
$endgroup$
– Ingolifs
Mar 31 at 22:36
1
$begingroup$
@Ingolifs Finger skin around a finger that is, and a perhaps a floppy fraying hand following.
$endgroup$
– Peter A. Schneider
Apr 2 at 7:43
add a comment |
$begingroup$
Propulsion comes from acceleration of a reaction mass.
In this case the grinding wheel serves two purposes:
- separate small bits of the workpiece from bulk at a slow and roughly uniform rate
- accelerate those bits by mechanical friction, in a similar way that a tennis ball launcher uses a matched pair of counter-propagating spinning wheels to shoot a box full of tennis balls one at at time in a controlled direction and speed.
As @Muze points out using a matched pair of counter-propagating spinning wheels would be important in spaceflight as well.
Step 1: requires a large amount of work and there's no reason to do that in space. You can produce the particle on the ground, so your propellant "tank" would be a feed system dispensing pellets or powder. They could be suspended in a fluid for easier feed and to avoid electrostatic clumping.
If you have to produce it in space, for example if you are reusing your lower stage as a reaction mass Horace style (Monty Python reference), then you can grind or otherwise form at a lower speed first with a separate wheel. Particles could be remelted in order to make them spherical, and then size-sorted for the following step.
Step 2: would conceptually be accomplished with a mechanism similar to that of a tennis ball launcher. Two counter-propagating wheels with the particle feed introduced in the small gap between the two wheels' surfaces. The particles would have to be monodipserse, meaning all of a fairly uniform size, and slightly smaller than the gap for good friction. Either the particles or the wheels would have to be elastically compressible enough so that there's a good grip for acceleration, and yet the surfaces should not be readily damaged during the process.
You could also very slightly incline the wheels such that if you had a sorted range of particle sizes they can all be introduced at the appropriate gap width.
However, as @Greg points out and then @ Thorondor demonstrates quantitatively, getting your wheels to spin at mach 10 or faster (for a (mass-)specific impulse or Isp of say 300 or so) is a real materials problem.
One possibility for propellant would be a maximal concentration (essentially HCP) liquid suspension of latex or polymer spheres which can be obtained highly monodisperse with sufficient money. If you don't have a lot of room for propellant, then perhaps metallic or metal oxide or nitride nanospheres can be produced by pyrolysis.
Horiba Scientific
GIF from Tennis ball machine DIY - part 1 a better view of a similar mechanism can be seen in Tennis Tutor Ball Machine mechanics in operation.
$endgroup$
Propulsion comes from acceleration of a reaction mass.
In this case the grinding wheel serves two purposes:
- separate small bits of the workpiece from bulk at a slow and roughly uniform rate
- accelerate those bits by mechanical friction, in a similar way that a tennis ball launcher uses a matched pair of counter-propagating spinning wheels to shoot a box full of tennis balls one at at time in a controlled direction and speed.
As @Muze points out using a matched pair of counter-propagating spinning wheels would be important in spaceflight as well.
Step 1: requires a large amount of work and there's no reason to do that in space. You can produce the particle on the ground, so your propellant "tank" would be a feed system dispensing pellets or powder. They could be suspended in a fluid for easier feed and to avoid electrostatic clumping.
If you have to produce it in space, for example if you are reusing your lower stage as a reaction mass Horace style (Monty Python reference), then you can grind or otherwise form at a lower speed first with a separate wheel. Particles could be remelted in order to make them spherical, and then size-sorted for the following step.
Step 2: would conceptually be accomplished with a mechanism similar to that of a tennis ball launcher. Two counter-propagating wheels with the particle feed introduced in the small gap between the two wheels' surfaces. The particles would have to be monodipserse, meaning all of a fairly uniform size, and slightly smaller than the gap for good friction. Either the particles or the wheels would have to be elastically compressible enough so that there's a good grip for acceleration, and yet the surfaces should not be readily damaged during the process.
You could also very slightly incline the wheels such that if you had a sorted range of particle sizes they can all be introduced at the appropriate gap width.
However, as @Greg points out and then @ Thorondor demonstrates quantitatively, getting your wheels to spin at mach 10 or faster (for a (mass-)specific impulse or Isp of say 300 or so) is a real materials problem.
One possibility for propellant would be a maximal concentration (essentially HCP) liquid suspension of latex or polymer spheres which can be obtained highly monodisperse with sufficient money. If you don't have a lot of room for propellant, then perhaps metallic or metal oxide or nitride nanospheres can be produced by pyrolysis.
Horiba Scientific
GIF from Tennis ball machine DIY - part 1 a better view of a similar mechanism can be seen in Tennis Tutor Ball Machine mechanics in operation.
edited Mar 31 at 6:37
answered Mar 31 at 4:59


uhohuhoh
40.5k18149511
40.5k18149511
7
$begingroup$
That device is an OSHA finger-trapping-hazard nighmare.
$endgroup$
– Richard
Mar 31 at 8:04
2
$begingroup$
@Richard it's at least a "DIY finger-trapping-hazard nightmare." ;-)
$endgroup$
– uhoh
Mar 31 at 8:07
5
$begingroup$
All reaction mass is good reaction mass, whether it's tennis balls or finger skin...
$endgroup$
– Ingolifs
Mar 31 at 22:36
1
$begingroup$
@Ingolifs Finger skin around a finger that is, and a perhaps a floppy fraying hand following.
$endgroup$
– Peter A. Schneider
Apr 2 at 7:43
add a comment |
7
$begingroup$
That device is an OSHA finger-trapping-hazard nighmare.
$endgroup$
– Richard
Mar 31 at 8:04
2
$begingroup$
@Richard it's at least a "DIY finger-trapping-hazard nightmare." ;-)
$endgroup$
– uhoh
Mar 31 at 8:07
5
$begingroup$
All reaction mass is good reaction mass, whether it's tennis balls or finger skin...
$endgroup$
– Ingolifs
Mar 31 at 22:36
1
$begingroup$
@Ingolifs Finger skin around a finger that is, and a perhaps a floppy fraying hand following.
$endgroup$
– Peter A. Schneider
Apr 2 at 7:43
7
7
$begingroup$
That device is an OSHA finger-trapping-hazard nighmare.
$endgroup$
– Richard
Mar 31 at 8:04
$begingroup$
That device is an OSHA finger-trapping-hazard nighmare.
$endgroup$
– Richard
Mar 31 at 8:04
2
2
$begingroup$
@Richard it's at least a "DIY finger-trapping-hazard nightmare." ;-)
$endgroup$
– uhoh
Mar 31 at 8:07
$begingroup$
@Richard it's at least a "DIY finger-trapping-hazard nightmare." ;-)
$endgroup$
– uhoh
Mar 31 at 8:07
5
5
$begingroup$
All reaction mass is good reaction mass, whether it's tennis balls or finger skin...
$endgroup$
– Ingolifs
Mar 31 at 22:36
$begingroup$
All reaction mass is good reaction mass, whether it's tennis balls or finger skin...
$endgroup$
– Ingolifs
Mar 31 at 22:36
1
1
$begingroup$
@Ingolifs Finger skin around a finger that is, and a perhaps a floppy fraying hand following.
$endgroup$
– Peter A. Schneider
Apr 2 at 7:43
$begingroup$
@Ingolifs Finger skin around a finger that is, and a perhaps a floppy fraying hand following.
$endgroup$
– Peter A. Schneider
Apr 2 at 7:43
add a comment |
$begingroup$
Even if feasible materials-wise, I suspect energy efficiency would be horrible. To spin something fast, where is that (rotational) energy going to come from? If you use an electric motor, you could just modify it to make a plasma drive and use it (more) directly. In your device a lot of that energy gets turned into heat (of the wheel) by friction. Presumably you could recycle that heat to a large extent, but the stuff to do that is already adding another layer of complexity.
$endgroup$
2
$begingroup$
You make a good point. What (might have been) pointed out to me and others in this comment and those that followed though, is that there can be situations in the future where raw material to be used as propellant is not scarce or limited to what's on board, but instead having a means to accelerate the raw material is the limiting factor.
$endgroup$
– uhoh
Mar 31 at 21:57
add a comment |
$begingroup$
Even if feasible materials-wise, I suspect energy efficiency would be horrible. To spin something fast, where is that (rotational) energy going to come from? If you use an electric motor, you could just modify it to make a plasma drive and use it (more) directly. In your device a lot of that energy gets turned into heat (of the wheel) by friction. Presumably you could recycle that heat to a large extent, but the stuff to do that is already adding another layer of complexity.
$endgroup$
2
$begingroup$
You make a good point. What (might have been) pointed out to me and others in this comment and those that followed though, is that there can be situations in the future where raw material to be used as propellant is not scarce or limited to what's on board, but instead having a means to accelerate the raw material is the limiting factor.
$endgroup$
– uhoh
Mar 31 at 21:57
add a comment |
$begingroup$
Even if feasible materials-wise, I suspect energy efficiency would be horrible. To spin something fast, where is that (rotational) energy going to come from? If you use an electric motor, you could just modify it to make a plasma drive and use it (more) directly. In your device a lot of that energy gets turned into heat (of the wheel) by friction. Presumably you could recycle that heat to a large extent, but the stuff to do that is already adding another layer of complexity.
$endgroup$
Even if feasible materials-wise, I suspect energy efficiency would be horrible. To spin something fast, where is that (rotational) energy going to come from? If you use an electric motor, you could just modify it to make a plasma drive and use it (more) directly. In your device a lot of that energy gets turned into heat (of the wheel) by friction. Presumably you could recycle that heat to a large extent, but the stuff to do that is already adding another layer of complexity.
edited Mar 31 at 18:47
answered Mar 31 at 18:34


FizzFizz
1515
1515
2
$begingroup$
You make a good point. What (might have been) pointed out to me and others in this comment and those that followed though, is that there can be situations in the future where raw material to be used as propellant is not scarce or limited to what's on board, but instead having a means to accelerate the raw material is the limiting factor.
$endgroup$
– uhoh
Mar 31 at 21:57
add a comment |
2
$begingroup$
You make a good point. What (might have been) pointed out to me and others in this comment and those that followed though, is that there can be situations in the future where raw material to be used as propellant is not scarce or limited to what's on board, but instead having a means to accelerate the raw material is the limiting factor.
$endgroup$
– uhoh
Mar 31 at 21:57
2
2
$begingroup$
You make a good point. What (might have been) pointed out to me and others in this comment and those that followed though, is that there can be situations in the future where raw material to be used as propellant is not scarce or limited to what's on board, but instead having a means to accelerate the raw material is the limiting factor.
$endgroup$
– uhoh
Mar 31 at 21:57
$begingroup$
You make a good point. What (might have been) pointed out to me and others in this comment and those that followed though, is that there can be situations in the future where raw material to be used as propellant is not scarce or limited to what's on board, but instead having a means to accelerate the raw material is the limiting factor.
$endgroup$
– uhoh
Mar 31 at 21:57
add a comment |
$begingroup$
The big challenge will be the forces on the outside of the wheel, ripping it apart.
We have to pin the numbers to something, and the easiest number to pin down would be the angular velocity. Zippie style uranium enrichment centrifuges operate around 1,500 revolutions per second, so they make a good benchmark. (Some turbochargers go faster, up to 4,800 revolutions per second, but they are rather small diameters, so easier to manufacture). 1500 rev/sec is about 9500 rad/sec. Since $v=romega$, we can solve for the radius of the wheel, $r=frac{v}{omega}$. Let's target a rather low velocity: 500m/s. Chemical rockets have exhaust velocities in the 2500-4500m/s range, but we can target a lower rate because we can always fuel up later. That pegs us as needing wheels on the order of 50cm in radius.
The exact structure of a Zippie style centrifuge is a closely guarded secret, but Wikipedia gives a notional centrifuge size of 20cm or smaller. This means our wheel is going to be withstanding forces roughly four times that of a nuclear enrichment centrifuge. Now mind you those centrifuges are carefully managed, sealed in vacuum chambers and levitated on magnetic bearings. The forces of accelerating mass with the edge of one of these wheels is going to be far greater. More importantly, they will be off axis, which is always tricky for a centrifuge.
So the material properties we need push the limits of what is used in enrichment centrifuges, just to get to one tenth of the ISP of a rocket. So the real question will be, are there mission plans where 1/10th of a rocket's ISP is useful, but where other technologies are insufficient.
$endgroup$
$begingroup$
Good reference to enrichment centrifuges. Please correct me if I'm wrong, but 500 m/s divided by 9500 rad/s gives 5.3 cm, not 50 cm. If that's right, then it's (in some way) easier to build than an enrichment centrifuge.
$endgroup$
– Everyday Astronaut
Apr 1 at 19:03
add a comment |
$begingroup$
The big challenge will be the forces on the outside of the wheel, ripping it apart.
We have to pin the numbers to something, and the easiest number to pin down would be the angular velocity. Zippie style uranium enrichment centrifuges operate around 1,500 revolutions per second, so they make a good benchmark. (Some turbochargers go faster, up to 4,800 revolutions per second, but they are rather small diameters, so easier to manufacture). 1500 rev/sec is about 9500 rad/sec. Since $v=romega$, we can solve for the radius of the wheel, $r=frac{v}{omega}$. Let's target a rather low velocity: 500m/s. Chemical rockets have exhaust velocities in the 2500-4500m/s range, but we can target a lower rate because we can always fuel up later. That pegs us as needing wheels on the order of 50cm in radius.
The exact structure of a Zippie style centrifuge is a closely guarded secret, but Wikipedia gives a notional centrifuge size of 20cm or smaller. This means our wheel is going to be withstanding forces roughly four times that of a nuclear enrichment centrifuge. Now mind you those centrifuges are carefully managed, sealed in vacuum chambers and levitated on magnetic bearings. The forces of accelerating mass with the edge of one of these wheels is going to be far greater. More importantly, they will be off axis, which is always tricky for a centrifuge.
So the material properties we need push the limits of what is used in enrichment centrifuges, just to get to one tenth of the ISP of a rocket. So the real question will be, are there mission plans where 1/10th of a rocket's ISP is useful, but where other technologies are insufficient.
$endgroup$
$begingroup$
Good reference to enrichment centrifuges. Please correct me if I'm wrong, but 500 m/s divided by 9500 rad/s gives 5.3 cm, not 50 cm. If that's right, then it's (in some way) easier to build than an enrichment centrifuge.
$endgroup$
– Everyday Astronaut
Apr 1 at 19:03
add a comment |
$begingroup$
The big challenge will be the forces on the outside of the wheel, ripping it apart.
We have to pin the numbers to something, and the easiest number to pin down would be the angular velocity. Zippie style uranium enrichment centrifuges operate around 1,500 revolutions per second, so they make a good benchmark. (Some turbochargers go faster, up to 4,800 revolutions per second, but they are rather small diameters, so easier to manufacture). 1500 rev/sec is about 9500 rad/sec. Since $v=romega$, we can solve for the radius of the wheel, $r=frac{v}{omega}$. Let's target a rather low velocity: 500m/s. Chemical rockets have exhaust velocities in the 2500-4500m/s range, but we can target a lower rate because we can always fuel up later. That pegs us as needing wheels on the order of 50cm in radius.
The exact structure of a Zippie style centrifuge is a closely guarded secret, but Wikipedia gives a notional centrifuge size of 20cm or smaller. This means our wheel is going to be withstanding forces roughly four times that of a nuclear enrichment centrifuge. Now mind you those centrifuges are carefully managed, sealed in vacuum chambers and levitated on magnetic bearings. The forces of accelerating mass with the edge of one of these wheels is going to be far greater. More importantly, they will be off axis, which is always tricky for a centrifuge.
So the material properties we need push the limits of what is used in enrichment centrifuges, just to get to one tenth of the ISP of a rocket. So the real question will be, are there mission plans where 1/10th of a rocket's ISP is useful, but where other technologies are insufficient.
$endgroup$
The big challenge will be the forces on the outside of the wheel, ripping it apart.
We have to pin the numbers to something, and the easiest number to pin down would be the angular velocity. Zippie style uranium enrichment centrifuges operate around 1,500 revolutions per second, so they make a good benchmark. (Some turbochargers go faster, up to 4,800 revolutions per second, but they are rather small diameters, so easier to manufacture). 1500 rev/sec is about 9500 rad/sec. Since $v=romega$, we can solve for the radius of the wheel, $r=frac{v}{omega}$. Let's target a rather low velocity: 500m/s. Chemical rockets have exhaust velocities in the 2500-4500m/s range, but we can target a lower rate because we can always fuel up later. That pegs us as needing wheels on the order of 50cm in radius.
The exact structure of a Zippie style centrifuge is a closely guarded secret, but Wikipedia gives a notional centrifuge size of 20cm or smaller. This means our wheel is going to be withstanding forces roughly four times that of a nuclear enrichment centrifuge. Now mind you those centrifuges are carefully managed, sealed in vacuum chambers and levitated on magnetic bearings. The forces of accelerating mass with the edge of one of these wheels is going to be far greater. More importantly, they will be off axis, which is always tricky for a centrifuge.
So the material properties we need push the limits of what is used in enrichment centrifuges, just to get to one tenth of the ISP of a rocket. So the real question will be, are there mission plans where 1/10th of a rocket's ISP is useful, but where other technologies are insufficient.
answered Apr 1 at 5:02


Cort AmmonCort Ammon
1,1991611
1,1991611
$begingroup$
Good reference to enrichment centrifuges. Please correct me if I'm wrong, but 500 m/s divided by 9500 rad/s gives 5.3 cm, not 50 cm. If that's right, then it's (in some way) easier to build than an enrichment centrifuge.
$endgroup$
– Everyday Astronaut
Apr 1 at 19:03
add a comment |
$begingroup$
Good reference to enrichment centrifuges. Please correct me if I'm wrong, but 500 m/s divided by 9500 rad/s gives 5.3 cm, not 50 cm. If that's right, then it's (in some way) easier to build than an enrichment centrifuge.
$endgroup$
– Everyday Astronaut
Apr 1 at 19:03
$begingroup$
Good reference to enrichment centrifuges. Please correct me if I'm wrong, but 500 m/s divided by 9500 rad/s gives 5.3 cm, not 50 cm. If that's right, then it's (in some way) easier to build than an enrichment centrifuge.
$endgroup$
– Everyday Astronaut
Apr 1 at 19:03
$begingroup$
Good reference to enrichment centrifuges. Please correct me if I'm wrong, but 500 m/s divided by 9500 rad/s gives 5.3 cm, not 50 cm. If that's right, then it's (in some way) easier to build than an enrichment centrifuge.
$endgroup$
– Everyday Astronaut
Apr 1 at 19:03
add a comment |
$begingroup$
A huge amount of energy would be wasted in the grinding process. Only a tiny fraction would be converted to kinetic energy: the rest would be wasted as heat, plus your grinder would wear down and you would have to have all sorts of complicated mechanisms to keep the thing running.
You could reduce the wear and the energy required to grind off the particles by using a weaker material.
But then you could just decide to not grind the particles off in the first place and throw powder out the back using a spinning wheel without the need to grind it.
But then you can just ionize the powder, eject the particles with an electric field and get rid of the wheel completely. It would be a lot more efficient.
Then you could replace the powder with xenon for more efficiency.
And now you have an ion drive and we already have those.
$endgroup$
1
$begingroup$
How does the heat energy relate to the kinetic energy in such a grinding process?
$endgroup$
– Everyday Astronaut
Apr 2 at 12:49
1
$begingroup$
Good question. I suppose the heat will come from friction which is required to grind off the material. Heat is the internal motion of the atoms in the particles as opposed to their external velocity. The ratio is going to depend on the strength of the material you are grinding, the optimal being no strength (i.e., a powder) which is what I was driving at.
$endgroup$
– rghome
Apr 2 at 14:14
1
$begingroup$
Totally agree with you. This will never have better ISP than ion thrusters. Its only advantage is its obvious refuelability, although I wouldn't rule that out for ion thrusters yet. Still, it would be nice if your qualitative estimate (“huge“) could be backed by some numbers. Also, I don't know about energy efficiency of ion thrusters.
$endgroup$
– Everyday Astronaut
Apr 2 at 18:30
1
$begingroup$
Honestly, for a grinder like in the picture, I think an efficiency of zero would be pretty accurate estimate. They normally consume a couple of hundred watts. If it removed 1 gram a second and ejected it at 100m/s (optimistic figures) that would be 5 watts of energy transferred.
$endgroup$
– rghome
Apr 2 at 21:55
add a comment |
$begingroup$
A huge amount of energy would be wasted in the grinding process. Only a tiny fraction would be converted to kinetic energy: the rest would be wasted as heat, plus your grinder would wear down and you would have to have all sorts of complicated mechanisms to keep the thing running.
You could reduce the wear and the energy required to grind off the particles by using a weaker material.
But then you could just decide to not grind the particles off in the first place and throw powder out the back using a spinning wheel without the need to grind it.
But then you can just ionize the powder, eject the particles with an electric field and get rid of the wheel completely. It would be a lot more efficient.
Then you could replace the powder with xenon for more efficiency.
And now you have an ion drive and we already have those.
$endgroup$
1
$begingroup$
How does the heat energy relate to the kinetic energy in such a grinding process?
$endgroup$
– Everyday Astronaut
Apr 2 at 12:49
1
$begingroup$
Good question. I suppose the heat will come from friction which is required to grind off the material. Heat is the internal motion of the atoms in the particles as opposed to their external velocity. The ratio is going to depend on the strength of the material you are grinding, the optimal being no strength (i.e., a powder) which is what I was driving at.
$endgroup$
– rghome
Apr 2 at 14:14
1
$begingroup$
Totally agree with you. This will never have better ISP than ion thrusters. Its only advantage is its obvious refuelability, although I wouldn't rule that out for ion thrusters yet. Still, it would be nice if your qualitative estimate (“huge“) could be backed by some numbers. Also, I don't know about energy efficiency of ion thrusters.
$endgroup$
– Everyday Astronaut
Apr 2 at 18:30
1
$begingroup$
Honestly, for a grinder like in the picture, I think an efficiency of zero would be pretty accurate estimate. They normally consume a couple of hundred watts. If it removed 1 gram a second and ejected it at 100m/s (optimistic figures) that would be 5 watts of energy transferred.
$endgroup$
– rghome
Apr 2 at 21:55
add a comment |
$begingroup$
A huge amount of energy would be wasted in the grinding process. Only a tiny fraction would be converted to kinetic energy: the rest would be wasted as heat, plus your grinder would wear down and you would have to have all sorts of complicated mechanisms to keep the thing running.
You could reduce the wear and the energy required to grind off the particles by using a weaker material.
But then you could just decide to not grind the particles off in the first place and throw powder out the back using a spinning wheel without the need to grind it.
But then you can just ionize the powder, eject the particles with an electric field and get rid of the wheel completely. It would be a lot more efficient.
Then you could replace the powder with xenon for more efficiency.
And now you have an ion drive and we already have those.
$endgroup$
A huge amount of energy would be wasted in the grinding process. Only a tiny fraction would be converted to kinetic energy: the rest would be wasted as heat, plus your grinder would wear down and you would have to have all sorts of complicated mechanisms to keep the thing running.
You could reduce the wear and the energy required to grind off the particles by using a weaker material.
But then you could just decide to not grind the particles off in the first place and throw powder out the back using a spinning wheel without the need to grind it.
But then you can just ionize the powder, eject the particles with an electric field and get rid of the wheel completely. It would be a lot more efficient.
Then you could replace the powder with xenon for more efficiency.
And now you have an ion drive and we already have those.
edited Apr 2 at 11:01
answered Apr 2 at 10:42
rghomerghome
20116
20116
1
$begingroup$
How does the heat energy relate to the kinetic energy in such a grinding process?
$endgroup$
– Everyday Astronaut
Apr 2 at 12:49
1
$begingroup$
Good question. I suppose the heat will come from friction which is required to grind off the material. Heat is the internal motion of the atoms in the particles as opposed to their external velocity. The ratio is going to depend on the strength of the material you are grinding, the optimal being no strength (i.e., a powder) which is what I was driving at.
$endgroup$
– rghome
Apr 2 at 14:14
1
$begingroup$
Totally agree with you. This will never have better ISP than ion thrusters. Its only advantage is its obvious refuelability, although I wouldn't rule that out for ion thrusters yet. Still, it would be nice if your qualitative estimate (“huge“) could be backed by some numbers. Also, I don't know about energy efficiency of ion thrusters.
$endgroup$
– Everyday Astronaut
Apr 2 at 18:30
1
$begingroup$
Honestly, for a grinder like in the picture, I think an efficiency of zero would be pretty accurate estimate. They normally consume a couple of hundred watts. If it removed 1 gram a second and ejected it at 100m/s (optimistic figures) that would be 5 watts of energy transferred.
$endgroup$
– rghome
Apr 2 at 21:55
add a comment |
1
$begingroup$
How does the heat energy relate to the kinetic energy in such a grinding process?
$endgroup$
– Everyday Astronaut
Apr 2 at 12:49
1
$begingroup$
Good question. I suppose the heat will come from friction which is required to grind off the material. Heat is the internal motion of the atoms in the particles as opposed to their external velocity. The ratio is going to depend on the strength of the material you are grinding, the optimal being no strength (i.e., a powder) which is what I was driving at.
$endgroup$
– rghome
Apr 2 at 14:14
1
$begingroup$
Totally agree with you. This will never have better ISP than ion thrusters. Its only advantage is its obvious refuelability, although I wouldn't rule that out for ion thrusters yet. Still, it would be nice if your qualitative estimate (“huge“) could be backed by some numbers. Also, I don't know about energy efficiency of ion thrusters.
$endgroup$
– Everyday Astronaut
Apr 2 at 18:30
1
$begingroup$
Honestly, for a grinder like in the picture, I think an efficiency of zero would be pretty accurate estimate. They normally consume a couple of hundred watts. If it removed 1 gram a second and ejected it at 100m/s (optimistic figures) that would be 5 watts of energy transferred.
$endgroup$
– rghome
Apr 2 at 21:55
1
1
$begingroup$
How does the heat energy relate to the kinetic energy in such a grinding process?
$endgroup$
– Everyday Astronaut
Apr 2 at 12:49
$begingroup$
How does the heat energy relate to the kinetic energy in such a grinding process?
$endgroup$
– Everyday Astronaut
Apr 2 at 12:49
1
1
$begingroup$
Good question. I suppose the heat will come from friction which is required to grind off the material. Heat is the internal motion of the atoms in the particles as opposed to their external velocity. The ratio is going to depend on the strength of the material you are grinding, the optimal being no strength (i.e., a powder) which is what I was driving at.
$endgroup$
– rghome
Apr 2 at 14:14
$begingroup$
Good question. I suppose the heat will come from friction which is required to grind off the material. Heat is the internal motion of the atoms in the particles as opposed to their external velocity. The ratio is going to depend on the strength of the material you are grinding, the optimal being no strength (i.e., a powder) which is what I was driving at.
$endgroup$
– rghome
Apr 2 at 14:14
1
1
$begingroup$
Totally agree with you. This will never have better ISP than ion thrusters. Its only advantage is its obvious refuelability, although I wouldn't rule that out for ion thrusters yet. Still, it would be nice if your qualitative estimate (“huge“) could be backed by some numbers. Also, I don't know about energy efficiency of ion thrusters.
$endgroup$
– Everyday Astronaut
Apr 2 at 18:30
$begingroup$
Totally agree with you. This will never have better ISP than ion thrusters. Its only advantage is its obvious refuelability, although I wouldn't rule that out for ion thrusters yet. Still, it would be nice if your qualitative estimate (“huge“) could be backed by some numbers. Also, I don't know about energy efficiency of ion thrusters.
$endgroup$
– Everyday Astronaut
Apr 2 at 18:30
1
1
$begingroup$
Honestly, for a grinder like in the picture, I think an efficiency of zero would be pretty accurate estimate. They normally consume a couple of hundred watts. If it removed 1 gram a second and ejected it at 100m/s (optimistic figures) that would be 5 watts of energy transferred.
$endgroup$
– rghome
Apr 2 at 21:55
$begingroup$
Honestly, for a grinder like in the picture, I think an efficiency of zero would be pretty accurate estimate. They normally consume a couple of hundred watts. If it removed 1 gram a second and ejected it at 100m/s (optimistic figures) that would be 5 watts of energy transferred.
$endgroup$
– rghome
Apr 2 at 21:55
add a comment |
$begingroup$
There are two considerations: one is ISP, which is discussed in several of the answers. The other is energy efficiency - how many joules of input energy end up converted to kinetic energy in the expelled propellant mass.
If you consider a typical rocket, energy efficiency is surprisingly high - IIRC something like 70% of the available chemical energy is converted to kinetic energy of propellant mass ejected along the thrust axis (the remainder is waste heat radiated away or components of propellant velocity perpendicular to the thrust axis).
Using a power plant e.g. nuclear to create electricity to drive a motor involves multiple conversion steps, each of which incurs losses. To begin with, a nuclear reactor itself creates heat which has to be converted to mechanical work (at best about 40% efficient IIRC) which is then converted to electricity (maybe 80%-90% efficient) and then to mechanical (again maybe 80%-90%).
Using a nuclear reaction to heat a propellant which you directly expel (nuclear rocket) gets you back to the same sort of energy efficiency as chemical rockets, but higher ISPs because you can potentially achieve higher temperatures.
$endgroup$
add a comment |
$begingroup$
There are two considerations: one is ISP, which is discussed in several of the answers. The other is energy efficiency - how many joules of input energy end up converted to kinetic energy in the expelled propellant mass.
If you consider a typical rocket, energy efficiency is surprisingly high - IIRC something like 70% of the available chemical energy is converted to kinetic energy of propellant mass ejected along the thrust axis (the remainder is waste heat radiated away or components of propellant velocity perpendicular to the thrust axis).
Using a power plant e.g. nuclear to create electricity to drive a motor involves multiple conversion steps, each of which incurs losses. To begin with, a nuclear reactor itself creates heat which has to be converted to mechanical work (at best about 40% efficient IIRC) which is then converted to electricity (maybe 80%-90% efficient) and then to mechanical (again maybe 80%-90%).
Using a nuclear reaction to heat a propellant which you directly expel (nuclear rocket) gets you back to the same sort of energy efficiency as chemical rockets, but higher ISPs because you can potentially achieve higher temperatures.
$endgroup$
add a comment |
$begingroup$
There are two considerations: one is ISP, which is discussed in several of the answers. The other is energy efficiency - how many joules of input energy end up converted to kinetic energy in the expelled propellant mass.
If you consider a typical rocket, energy efficiency is surprisingly high - IIRC something like 70% of the available chemical energy is converted to kinetic energy of propellant mass ejected along the thrust axis (the remainder is waste heat radiated away or components of propellant velocity perpendicular to the thrust axis).
Using a power plant e.g. nuclear to create electricity to drive a motor involves multiple conversion steps, each of which incurs losses. To begin with, a nuclear reactor itself creates heat which has to be converted to mechanical work (at best about 40% efficient IIRC) which is then converted to electricity (maybe 80%-90% efficient) and then to mechanical (again maybe 80%-90%).
Using a nuclear reaction to heat a propellant which you directly expel (nuclear rocket) gets you back to the same sort of energy efficiency as chemical rockets, but higher ISPs because you can potentially achieve higher temperatures.
$endgroup$
There are two considerations: one is ISP, which is discussed in several of the answers. The other is energy efficiency - how many joules of input energy end up converted to kinetic energy in the expelled propellant mass.
If you consider a typical rocket, energy efficiency is surprisingly high - IIRC something like 70% of the available chemical energy is converted to kinetic energy of propellant mass ejected along the thrust axis (the remainder is waste heat radiated away or components of propellant velocity perpendicular to the thrust axis).
Using a power plant e.g. nuclear to create electricity to drive a motor involves multiple conversion steps, each of which incurs losses. To begin with, a nuclear reactor itself creates heat which has to be converted to mechanical work (at best about 40% efficient IIRC) which is then converted to electricity (maybe 80%-90% efficient) and then to mechanical (again maybe 80%-90%).
Using a nuclear reaction to heat a propellant which you directly expel (nuclear rocket) gets you back to the same sort of energy efficiency as chemical rockets, but higher ISPs because you can potentially achieve higher temperatures.
answered Mar 31 at 19:04
Anthony XAnthony X
9,43513681
9,43513681
add a comment |
add a comment |
protected by called2voyage♦ Apr 2 at 13:07
Thank you for your interest in this question.
Because it has attracted low-quality or spam answers that had to be removed, posting an answer now requires 10 reputation on this site (the association bonus does not count).
Would you like to answer one of these unanswered questions instead?
5 5Uc7B 8tYy9mk5pEDF3pzrNgF3MKChY3,5en5iPwyYCMBN5tAZyrCt8,bi DxAv3uIlHT d zJI8y,kUp CwO6
12
$begingroup$
It would need 2 grinding machines for a counter balance.
$endgroup$
– Muze
Mar 30 at 21:58
18
$begingroup$
"The amount of propulsion produced at any one time would be achieved by increasing/decreasing the rotational speed of the grinding wheel." -- More likely, by utilizing a duty cycle of 100% on/off, otherwise you're wasting your fuel by not ejecting it with full force.
$endgroup$
– Jacob Krall
Mar 31 at 4:33
1
$begingroup$
@JacobKrall good point, or just by varying the feed rate of the work piece against the wheel.
$endgroup$
– uhoh
Mar 31 at 6:39
2
$begingroup$
What are you using to power the wheel? Why don't you use that to power the ship directly?
$endgroup$
– David Richerby
Apr 1 at 11:24
1
$begingroup$
FWIW: youtu.be/SAHmTQWsxeM?t=171
Lighter Exhaust Gas == Higher Velocity
(at the same temperature). I'm guessing that would also apply to solids.$endgroup$
– PEEJWEEJ
Apr 1 at 16:00